
160+ Pharmaceutical Interview Questions and Answers for Oral Solid Formulations
This page covers most of the interview questions and answers during a technical round in Production Oral Solid Dosage. The interview questions cover questions from basic to advance level of technical aspects. These interview questions and answers will help to crack an interview, enhance your knowledge, and also be helpful for the interviewer who is involved in the recruitment process.
The topics covered here are the Granulation process, the Tablet Compression process, the Coating process, and associated topics. In addition, the interview questions and answers cover various equipment used for the manufacturing process of solid oral formulation such as Compression Machine, Coating Machine, Graduation equipment, and supporting accessories.
You will find it much more enjoyable while going through these interview questions and answers. So enjoy learning, and best of luck with your interview! Happy Learning.
1. What is the granulation end point?
End-point can be defined by the formulator as a target particle size mean or distribution. [Reference: 5]
The agglomerate growth in wet granulation processes depend mainly on rheology of the wet powder mass, as an adequate consistency is necessary for a controllable coalescence and growth of smaller agglomerates into larger agglomerates.[Reference: 6]
2. Method for end point detection for wet granulation process.
i. Banana breaking test or Hand squeeze test
ii. Ampere load method
iii. Measurements of power consumption of the mixer motor
iv. Impeller Torque
v. Binder solution addition and measurement of Loss On Drying (LOD)
vi. Torque value
3. What is the Banana breaking method or Hand squeeze test for determination of granulation end point?
Wear hand gloves, take one handful of wet mass in the palm and press to make a lump. Open the palm and break the lump by pressing the thumb at the center of the lump.
4. What is the principle of metal detectors?
The operation of these metal detectors is based on the principles of electromagnetic induction. Metal detectors contain one or more inductor coils that are used to interact with metallic elements. Metallic contaminant in the product creates a high frequency magnetic field within the detector coil, which in turn activates a reject flap.
5. What is the fail safe mechanism of metal detectors?
When a metal detector gets off because of power failure or inadvertently did not start before the start of the batch, the flap should remain open so that tablets get rejected. It must be challenged at regular intervals (e.g.: start, intermittently and at the end of shift) to make sure they are effective.
6. What are typical standards used for the challenge of metal detectors?
Tablet: Ferrous – 0.3 mm, Non-ferrous – 0.3 mm, Stainless Steel – 0.5 mm, Plain (without metal as a blank)
Capsule: Ferrous – 0.1 mm, Non-ferrous – 0.15 mm, Stainless Steel – 0.2 mm, Plain (without metal as a blank)
7. What is tablet tooling?
Tooling consists of three parts.
i. Upper punch, ii. Lower punch, and iii. Die
8. What is the meaning of one set of tablet tooling?
One set consists of one Upper punch, one Lower punch and a Die.
9. What is a tooling station?
The place where one set accommodates the tablet press.
10. Explain parts of tablet tooling.
Punch terminologies:


Head: Head is the top part of upper and lower punch which contacts the machine’s cams and the pressure rollers apply the pressure to the head to compress the tablets.
Head flat or Dwell Flat: Top flat area of the head. Compression force applied through the upper punch head flat and ejection pressure applied through the head flat of lower punches. Dwell time for compression is determined based on the Head flat hence, it is also called Dwell Flat.
Outside head angle: The area touches the pressure roller during compression operation.
Inside head angle: The part of the punch head helps the upper punch to lift after compression of tablets and helps in pulling down the lower punches after ejection.
Neck: The part between head and barrel. Allow a clear path to the cam.
Barrel: Allows punch to do vertical up and down movement.
Stem: Area from tip end to barrel edge.
Tip: It is the lowest portion of the punch which is responsible for shape, size and profile of the tablet.
Tip face or cup: Outer part of the tip which gives shape to the tablet. The face also will have embossing depending on the need of the tablet requirement.
Tip length: The straight portion of the stem or tip.
Tip straight: The portion of tip towards the face having a higher diameter of the tip.
Tip relief: Tip part other than the tip straight.
Working length: This is the distance from the head flat to bottom of the cup.
Overall length: Length from punch head flat to the tip.
Key or woodruff key: An elevated portion in the middle of the punch barrel. The key with upper punches for shaped tablets to prevent punch rotation when the punch is out of the die.
Types of heads: Domed head and Flat head
Difference between Flat head and Domed head – Domed head punches have smaller flat heads.


The extended head flat offers multiple benefits, including a longer dwell time (the time the head flat spends in contact with the pressure roll) at a given press speed to better compact poorly compressible products. The longer dwell time may even reduce the amount of force required to attain specific tablet hardness.
Whereas, round extended head flats don’t require keyed tooling as oval ones do, and that allows them to be used on multiple makes and models of tablet presses.
Dwell time: It is the time the head flat spends in contact with the pressure roller.
Land: The area between the outer part of the punch cup and the outside edge of the punch tip.
Cup depth: Distance between tip edge to the center point of the cup.
Barrel chamfer: Chamfers at the ends of the punch barrel.
Die terminologies:

Clearance: pace between die bore diameter and punch tip diameter
Die Bore: It is the cavity of the die where granules are converted into tablets.
Die height or overall length: The height from top to bottom face of the die.
Die chamfer: This is the angle of the die bore at entry point. It guides the upper punch into the die bore.
Die groove and die lock: The radial groove around the die outer diameter requires locking the die into the turret with the help of die lock.
Die taper: Taper is a feature that increases the bore size at the top of the die then nominal bore size. It helps to release air from the die cavity during the compression. The feature helps to reduce tablet defects, such as capping and lamination.
Annealing: This is a heat treatment process to reduce the hardness to make it more workable. The processing done fragile punch tips to decrease the hardness of the punch cups which helps in reducing punch tip fracturing.
11. Describe tablet tooling standards?
There are two types of standards for tablet tooling:
i. US specification provided by Tableting Specification Manual (TSM) (This is the only tooling specifications are the only published standards for the tablet compression industry). The standard is established by the American Pharmacists Association (APhA),
ii. European standard known as the EU, or “Euronorm” standard.
EU, or Euronorm standard tool configurations are not published or governed by an organization or association. The EU standard is the most common tooling configuration used outside the U.S. [Reference: 7]
12. Differences between TSM and EU Tooling Configurations
Tableting Specification Manual (TSM) Tooling Configurations | EU Tooling Configurations |
Angled top profile | Domed head profile |
Inside head angle for “B” punches is 37° | Inside head angle for “B” punches is 30° |
Overall head thickness is greater in both “B” and “D” | Overall head thickness is lesser in both “B” and “D” |
Overall punch length of the TSM tool is 0.010 inches shorter than the EU | Overall punch length of the EU tool is 0.010 inches longer than the TSM |
13. What is the type of tablet tooling for a compression machine with die and punch dimension?
There are the following six types of tablet tooling and its dimensions.
Tooling specification | Nominal punch barrel diameter (mm) | Nominal punch die diameter (mm) | Maximum tablet diameter for round tablet (mm) | Maximum tablet diameter for shaped tablet (mm) |
TSM or EU B | 19 | 30.16 | 16 | 16 |
TSM or EU D | 25.35 | 38.1 | 25 | 25 |
TSM or EU BB | 19 | 24 | 13 | 14 |
TSM or EU DB | 25.35 | 30.16 | 19 | 19 |
TSM or EU BBS | 19 | 21 | 12 | 13 |
TSM or EU A | 12.7 | 17 | 8 | 8 |
14. What is the choice for material of construction (MoC) of Die and Punch?
i. OHNS (T) Oil Hardened Non shrinking steel (Tungsten) – AISI 01 (American Iron and Steel Institute)
ii. HCHC – High carbon High chromium steel – AISI D3
15. What is the choice for material of construction (MoC) of Turret?
Three piece turret having the center die table of SS 316 and the Upper and lower piece of Spheroidal Graphite Iron (SG Iron) with ELNP (ELECTROLESS NICKEL PLATING) Coating.
16. What is the chemical composition of OHNS steel?
Element | Content (%) |
C | 0.85-1.00 |
Si | 0.15-0.35 |
Mn | 1.00-1.20 |
P | 0.03 Max |
S | 0.03 Max |
Cr | 0.50-0.70 |
W | 0.50-0.70 |
17. How much is the lifespan of the die and punches?
The life span of punches and dies is purely depending on materials of construction (MoC) as well as usage and handling.
OHNS Punches and HCHC Dies: 4 million tablets
HCHC Punches and HCHC Dies: 8 Million tablets Complete hard chrome plating punches and
HCHC dies: 10 Million tablets
18. How to maintain Punches and Dies?
The maintenance of compression tooling becomes easy by following these mentioned steps:
Step 1: Cleaning during every product change over or on a periodic basis. They can be wiped with IPA and dried using a lint free cloth.
Step 2: Periodic evaluation to increase their shelf life. Industry practice is to
Step 3: The regular visual inspection of the tooling should be done after each cleaning to check for physical damages to head, tip, die, and embossing, debossing using Magnifying glass.
Step 4: Periodic inspection of the punch set should be done using measuring tools. Frequency for die and punch inspection should be such that first inspection after procurement should be done after 3 million tablet compression using each tool set and subsequently after each million.
Step 5: Compression punch set should be lubricated to decrease friction and enhance the operational activity of the tablet compression machine. A non-toxic, FDA approved oils and greases should be used for preservation and lubrication purposes. Storage of tooling should be done in the safe and moisture-free place.
19. What should be available in a punch set/ tablet tooling inspection kit?
1 | Dial gauge compactor stand with a least count of 0.001 inch |
2 | Micrometer Range from 0.25 mm with least count : 0.01 mm |
3 | Punch holding bushes for B type punch and D type of punch |
4 | Punch height gauge |
5 | Die Outer diameter block for all types of die i.e. D, B, BB, DB etc. |
6 | Magnetic V – block |
7 | GO – NO GO gauges |
8 | Magnifying Glass |
9 | Die Pocket Cleaner |
20. Explain about the punch set/ tablet tooling inspection program?
i. Height uniformity of the punches
ii. Punch body to punch tip concentricity
iii. Die bore Go / No go status
iv. Other dimensions as per the drawing
v. Punch tip to die before clearance
vi. Hollow penetration of the punches
vii. Die outdoor diameter consistency
viii. Die height regularity
ix. Die hole GO and NO GO examination
x. Die internal diameter to outer diameter concentricity
21. Issue that may arise after prolonged use for punch set/ tablet tooling.
i. Tablet weight difference
ii. Tablet hardness difference
iii. Powder leakage from lower punch or collar formation
iv. Twisting of small size punch tips
22. Commonly used material of construction in the pharmaceutical industry for equipment manufacturing?
i. Commonly used materials of construction in the pharmaceutical industry for product contact parts are Stainless steel 316, 316 L, Toughened glass, Silicon, Food grade Teflon etc.
ii. Commonly used materials of construction in the pharmaceutical industry for non-product contact parts are Stainless steel 304, 304 L, Teflon, Anodized or powder coated aluminum, brass etc.
23. Explain characteristics of different grades of stainless steel material.
Following are the different types of types of Stainless and similar material with its characteristics.
Stainless and similar material | Application for the different types of environment |
Hastelloy C276 | Excellent corrosion resistance in a wide range of severe environments |
316, 316L | Chemical corrosion |
304, Custom 450 | Medium Corrosion |
430, 431, Custom 455 | Industry polluted air |
405, 410, 420, 440 | Clean air |
24. Explain most commonly used stainless steel for pharmaceutical industry and its attributes.
Following most commonly used stainless steel for the pharmaceutical industry and its attributes.
Commonly known names | UNS | EN | Attributes |
304 | S30400 | 1.4301 | Good at general corrosion resistance to acidic as well as caustic material |
304L | S30403 | 1.4307 | Good at general corrosion resistance to acidic as well as caustic material with low carbon and improved performance |
316 | S31600 | 1.4401/ 1.4436 | Improved corrosion resistance to most acidic as well as caustic material with high temperature or chloride present |
316L | S31603 | 1.4404/ 1.4432 | Improved corrosion resistance to most acidic as well as caustic material with high temperature or chloride present with low carbon and improved performance |
25. How to distinguish SS 202, SS 304 and SS 316 grade stainless steel?
Using molybdenum detection electrolyte kit. To know how to perform the test, Click Here.
26. What is the composition of SS 304, SS 304L, SS 316, and SS 316L?
Following are the composition of SS 304, SS 304L, SS 316, and SS 316L

27. What is the meaning of Suffix L in SS 316L and SS 304L?
Suffix L for SS 316 and SS 304 represents low carbon content. Standard grade consists of ≤ 0.08 % carbon and low carbon grade consists of ≤ 0.03 % carbon content.
28. What are the different types of stainless steel in terms of material composition?

29. What is Hastelloy?
Hastelloy is a nickel-molybdenum-chromium superalloy with an addition of tungsten designed to have excellent corrosion resistance in a wide range of severe environments. The high nickel and molybdenum contents make the nickel steel alloy especially resistant to pitting and crevice corrosion in reducing environments while chromium conveys resistance to oxidizing media. The low carbon content minimizes carbide precipitation during welding to maintain corrosion resistance in as-welded structures. This nickel alloy is resistant to the formation of grain boundary precipitates in the weld heat-affected zone, thus making it suitable for most chemical process application in an as welded condition.
Source: megamex.com
30. In what applications is Hastelloy used?
i. Pharmaceutical and food processing equipment
ii. Chemical processing components like heat exchangers, reaction vessels, evaporators, and transfer piping
iii. Sour gas wells
iv. Waste treatment
31. Which are typical in-process control tests for tablets?
Dimensions
Hardness
Friability
Thickness
Disintegration
Weight variation
Content uniformity
Dissolution
Leakage testing for strip and blister packaging
Checking printing matter during packaging
Physical appearance of packs
32. Explain Disintegration time (DT) of different types of tablets?
Disintegration time (DT) of different types of tablets is as follows.
Types of tablets | Disintegration time (DT) |
Uncoated | 15 minutes |
Plain coated tablet | 60 minutes |
Enteric coated tablet | 3 hours |
Dispersible tablet | 3 minutes |
Effervescent tablet | ˂ 3 minutes |
Sublingual tablet | 4 hours |
Buccal tablet | 4 hours |
Vaginal tablet | 60 minutes |
Chewable tablet | not required |
33. What are the types of hardness testers?
Manual hardness tester
Monsanto tester

Pfizer tester

Strong-cobb

Automatic hardness testers
Erweka tester
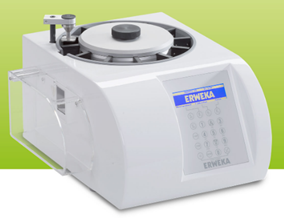
Dr. Schleuniger tester

34. Which instruments are used for testing tablet dimension?
A. Vernier caliper

1. Outside jaws: used to measure external length
2. Inside jaws: used to measure internal length
3. Depth probe: used to measure depth
4. Main scale (cm)
5. Main scale (inch)
6. Vernier (cm)
7. Vernier (inch)
8. Retainer: used to block/release movable part
B. Micrometer screw gauge

35. Which instruments are used for testing of tablet friability?
Roche friabilator is used for testing of tablet friability.
36. Explain the construction of tablet friability tester, testing process and limit.
i. Plastic chamber that revolves at 25 rpm
ii. For testing it operates for 100 revolutions
iii. Dropping the tablets from a Distance of 6 inches in the tester
iv. The tablets are weighed before and after rotation. De-dust tablets after rotation. Perform calculation in percentage weight loss.
v. Limit of friability testing is NMT 1.0 %
37. What is Disintegration Time (DT) Test?
Disintegration time is time taken to break down the tablets into granules or primary powder particles.
38. Explain the tablet disintegration tester parts.
i. Basket rack assembly
ii. A suitable vessel for the immersion liquid
iii. Heater for fluid heating between 35°C and 39°C
iv. Basket in the immersion in fluid at frequency rate between 28 and 32 cpm (Cycle per minute)
v. Distance of up and down not less than 5 cm and not more than 6 cm


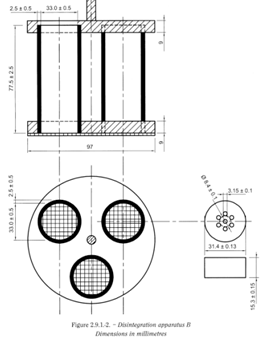
39. What are the common tablet defects at compression stage?
Weight variation
High friability
High or low hardness (resistance to crushing)
Sticking
Picking
Capping
Laminating
Chipping
Mottling
Double press or impression
Cracking
Binding
Edging or Flashing of tablet
Disintegration time abnormality
Black Spot/ particles/ fiber
Improper embossing or debossing
Layer separation
Improper Layers
40. What are the different types of tablet coating defects?
Blistering
Chipping
Cratering
Sticking or Picking
Pitting
Blooming
Blushing
Color Variation
Infilling
Orange Peel or Roughness
Cracking or Splitting
Twinning Erosion
Bridging
41. Definitions of tablet defects at compression stage.
Weight variation: Individual weight of tablet outside of the accepted criteria.
High friability: The condition of tablets being friable. The tendency of tablets to break into smaller pieces or weight loss of powder from the surface of the tablets due to mechanical action such as transportation conditions. When percentage loss is more than 1%, it is considered as high friability.
To view images of tablet defects and to download high resolution poster, CLICK HERE
High or low hardness (resistance to crushing): Individual hardness of tablets is outside the accepted limit (upper limit or lower limit). Hardness limits are determined during the development phase of the product.
Sticking: Sticking is a defect of the tablet wherein the portion tablet surface sticks to the face of the punch or to the die wall during tablet compression activity.
Picking: Picking is a counter part of the sticking. When part of the tablet surface sticks to the punch or to the die wall, the produced tablets are with a pitted surface instead of a smooth surface.
Capping: Capping (or splitting) is a term used to describe the partial or complete separation of the upper or lower segment of the tablet horizontally from the main body of a tablet during ejection from the tablet press.
Laminating: Laminating of tablets means separation of a tablet into two or more different parallel layers.
Chipping: Chipping of tablets is the breaking of tablet edges during manufacturing or handling.
Mottling: Mottling of tablet refers to unequal or nonuniform distribution of color on the tablet surface.
Double press or impression: Double impression is a tablet defect where an embossing or break or score line appears two times on the tablet surface.
Cracking: Cracking of tablets means small fine cracks on the upper and lower central surface of the tablets and sometimes seen on the side wall.
Binding: The term binding is used when tablets stick to the die and do not eject properly out of the die.
Edging or Flashing of tablet: Edging or Flashing means observation of burrs or sharp edges on the edges of tablet.
Disintegration time abnormality – Too fast or too slow disintegration of tablets.
Black Spot/ particles/ fiber – Observation of black spot or particles or fiber which could be indigenous or foreign matter or contaminant.
Improper embossing or debossing: The defect because of improper embossing or debossing of letter, logo or monogram.
Layer separation: Layer separation is the defect of a tablet where layers of tablet get separated. This is usually seen in tablets such as bilayer tablets.
Improper Layers: Improper Layers mainly appear in layered tablets such as bilayer tablets. In this type of defect, the layer does not distinguish sharply.
42. What are the different types of tablet coating defects?
Blistering: Blistering means blistering of a surface film appears when film becomes detached from the tablet’s substrate.
Chipping: Chipping means dented and chipped film mostly on the edges of the tablet.
Cratering: Cratering means volcanic-like cratering happens exposing the tablet surface.
Sticking or Picking: Sticking or picking means sticking of film with each other or with the coating pan resulting in some of the tablet pieces being detached from the core.
Pitting: Pitting is the deformation of the core of the tablet without any visible signs of disruption of the film coating.
Blooming: Blooming is the fading or dulling of a tablet color after it is stored for a prolonged period at a high temperature.
Blushing: Blushing is described as the appearance of white specks or a haziness in the film.
Color Variation: Color variation of tablet film.
Infilling: This refers to the filling of intagliations – i.e., the distinctive words or symbols formed on the tablet.
Orange Peel or Roughness: When film having a rough surface or having a matt surface rather than glossy texture. It appears the same as an orange.
Cracking or Splitting: The cracking defect is observed when the film coating of the tablet cracks in the crown area or splits around the edges.
Twinning: Twinning is when two tablets stick together.
Erosion: Coating gets removed from the surface due to friction between tablets.
Bridging: When coating material fills in the logo or letter, bridging occurs.
43. Explain the remediation for various types of tablet defects.

44. What are the different sizes of hard gelatin capsules?
The capsule sizes are 000, 00, 0, 1, 2, 3, 4, and 5 from the largest to the smallest. There are few special sizes of capsules available such as 2el, 1el, 0el, 0el+, 0xel, 00el etc. Details are tabulated below.


45. What are the US Mesh size and corresponding micron, mm and inch for commonly used sieves, provide a few examples?
U.S. Mesh | Microns | Inches | Millimeters |
3 | 6730 | 0.2650 | 6.730 |
4 | 4760 | 0.1879 | 4.760 |
5 | 4000 | 0.1570 | 4.000 |
6 | 3360 | 0.1320 | 3.360 |
7 | 2830 | 0.1110 | 2.830 |
8 | 2380 | 0.0937 | 2.380 |
10 | 2000 | 0.0787 | 2.000 |
12 | 1680 | 0.0661 | 1.680 |
14 | 1410 | 0.0555 | 1.410 |
16 | 1190 | 0.0469 | 1.190 |
18 | 1000 | 0.0394 | 1.000 |
20 | 840 | 0.0311 | 0.841 |
25 | 707 | 0.0280 | 0.707 |
30 | 595 | 0.0232 | 0.595 |
35 | 500 | 0.0197 | 0.500 |
40 | 400 | 0.0165 | 0.400 |
45 | 354 | 0.0138 | 0.354 |
50 | 297 | 0.0117 | 0.297 |
60 | 250 | 0.0098 | 0.250 |
70 | 210 | 0.0083 | 0.210 |
80 | 177 | 0.007 | 0.177 |
100 | 149 | 0.0059 | 0.149 |
120 | 125 | 0.0049 | 0.125 |
140 | 105 | 0.0041 | 0.105 |
170 | 88 | 0.0035 | 0.088 |
200 | 74 | 0.0029 | 0.074 |
230 | 63 | 0.0024 | 0.063 |
270 | 53 | 0.0021 | 0.053 |
325 | 44 | 0.0017 | 0.044 |
400 | 37 | 0.0015 | 0.037 |
450 | 32 | 0.0013 | 0.032 |
500 | 25 | 0.0010 | 0.025 |
550 | 25 | 0.0009 | 0.023 |
635 | 20 | 0.0008 | 0.020 |
800 | 15 | 0.0006 | 0.015 |
1250 | 10 | 0.0004 | 0.010 |
Reference: ASTM E11
46. Give examples of sieve size and corresponding number of Apertures per Linear inch.
Sr. No. | Sieve Size | Number of Apertures per Linear Inch |
1 | 10 # | 9-11 |
2 | 12# | 11-13 |
3 | 14# | 13-15 |
4 | 16# | 15-17 |
5 | 20# | 19-21 |
6 | 24# | 23-25 |
7 | 30# | 28-32 |
8 | 40# | 38-42 |
9 | 60# | 57-63 |
10 | 80# | 77-83 |
11 | 100# | 97-103 |
47. What is the aperture size of the screen?
The size of a square opening (length of clear space between individual wires) is called the aperture size of the screen.
48. What is the Mesh number of screens?
Mesh number of screens is defined as the number of aperture or opening per linear inch of the screen. E.g. A screen having 10 square openings per inch is said to have Mesh no. 10. Higher the mesh number, smaller the aperture size of the screen.
49. What is the broad classification of Granulation techniques?
Granulation technique is broadly classified into two types as follows:
(i) Dry granulation
a. Slugging technique
b. Roller compaction
c. Pneumatic dry granulation
(ii) Wet granulation
a. Steam granulation
b. Reverse wet granulation
c. Moisture-Activated Dry Granulation
d. Thermal adhesion granulation
e. Melt granulation
f. Freeze granulation
g. Foam granulation
50. What are the equipment used during the Wet Granulation Process?
Depending on process, batch size and type of process steps, following equipment are used during the Wet Granulation Process.
Low Shear mixer/ granulator
High Shear mixer/ granulator OR Rapid Mixture granulator
Fluid-Bed granulator/ dryer,
Spray Dryer,
Extruders and Spheronizer
Vibratory sifter
Cutting mills such as Multimill, Co-mill, Pin Mill etc.
Hammer mill
51. What are the equipment used during the Dry Granulation Process?
Depending on process, batch size and type of process steps, following equipment are used during the Dry Granulation Process.
Role com
Low Shear mixer/ granulator
High Shear mixer/ granulator OR Rapid Mixture granulator
Vibratory sifter
Cutting mills such as Multimill, Co-mill, Pin Mill etc.
Roller Compactor Granulator
Compression machine to generate slugs
52. What is the most commonly used testing method to determine powder flow?
There are four commonly used methods for testing powder flow:
(1) Angle of repose
(2) Compressibility index or Hausner ratio
(3) Flow rate through an orifice
(4) Shear cell
Reference: General Chapters: <1174> POWDER FLOW
53. What is Angle of Repose?
Definition of Angle of Repose: The angle of repose is a relatively simple technique for estimating the flow properties of a powder. It is determined by allowing a powder to flow through a funnel and fall freely onto a fixed diameter base. The height and diameter of the resulting cone are measured. For further reading on Angle of Repose and download free excel, click on this link.
54. What is the Compressibility index and what is Hausner Ratio?
Definition of Compressibility index: The Compressibility Index (Carr Compressibility Index) is a measure of the tendency of a powder to be compressed. It is a measure of the powder’s ability to settle, and it permits an assessment of the relative importance of interparticulate interactions.
Definition of Hausner Ratio: The Hausner Ratio is measures that can be used to predict the tendency of a given powder sample to be compressed. Hausner Ratio reflects the importance of interparticulate interactions.
55. What is the disintegration time of Chewable Tablets?
Disintegration time test is not applicable for chewable tablets.
56. What is the standard number of rotations used for friability test?
100 Revolutions / 4 Minutes, 25 rotations per minute
57. What is the fall height of the tablets in the friabilator during friability testing?
Fall height of the tablets is in the friabilator is 154.0 – 158.0 mm (156.0 ± 2.0 mm)
58. Which capsule is bigger in size – size ‘0’ or size ‘1’?
‘0’ size
59. How many tablets shall be taken for checking friability?
6.5 g for the tablets with unit mass equal or less than 650 mg. For tablets with unit mass more than 650 mg, it requires 10 tablets.
60. What is the mesh aperture of DT apparatus?
Mesh aperture of DT apparatus is #10. That is 1.8 -2.2 mm.
61. What is the standard frequency of upward and downward movement of a basket-rack assembly in a DT apparatus?
28 – 32 cycles/minute
62. What are the parameters tested during the calibrating DT apparatus?
Parameters covered during the DT apparatus calibration are as follows
(1) Number of strokes per minute (Limit: 29-32 cycles/min)
(2) Temperature by probe and standard thermometer (Limit: 37 ± 1 °C). (3) Distance travelled by basket (Limit: 53 -57 mm)
63. What is the Disintegration time for different types of tablets?
Type of Tablets | Disintegration time |
Uncoated Tablets | 15 minutes |
Film-coated | 30 minutes |
Other coated tablets | 60 minutes |
Enteric-coated Tablets | |
0.1M hydrochloric acid | Should not disintegrate in 120 minutes |
Phosphate buffer pH 6.8, | 60 minutes. |
Dispersible and Soluble Tablets | within 3 minutes |
Effervescent Tablets | 5 minutes |
Chewable tablets | Not applicable |
64. What are the different clean room conditions? Explain it.
There are three conditions of clean rooms – as built, at rest and in-operation.
As built:

Condition where the installation is complete with all services connected and functioning but with no production equipment, materials, or personnel present.
At rest:

Condition where the installation is complete with equipment installed and operating in a manner agreed upon by the customer and supplier, but with no personnel present.
In operational:

This condition relates to carrying out room classification tests with the normal production process with equipment in operation, and the normal staff present in the room.
Reference: WHO Working document QAS/02.048/Rev.2
65. What are the different types of air locks? Explain it.
There are three types of air locks, Cascade airlock, Sink airlock and Bubble airlock.

Cascade airlock: high pressure on one side of the airlock and low pressure on the other side.
Bubble Airlock: high pressure inside the airlock and low pressure on both outer sides.
Sink Airlock: low pressure inside the airlock and high pressure on both outer sides.
Reference: WHO Working document QAS/02.048/Rev.2
66. What should be the differential pressure between two adjacent clean room zones?
The most widely accepted pressure differential to achieve containment between the two adjacent zones is 15 Pa, but pressure differentials of between 5 Pa and 20 Pa could be acceptable.
Where the design pressure differential is too low and tolerances are at opposite extremities, a flow reversal can take place. E.g. where a control tolerance of ±3 Pa is specified, the implications of the upper and lower tolerances on containment should be evaluated.
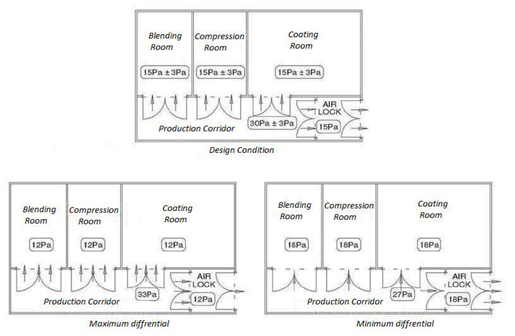
67. Comparison of pascals to mm of water?
Pascals to Millimeters of water formula
mm H2O =Pa * 0.10197
Pascals (Pa)
Millimeters of water (mm H2O)
Pascals | Millimeters of water | Pascals | Millimeters of water | Pascals | Millimeters of water |
1Pa | 0.10mm H2O | 16Pa | 1.63mm H2O | 31Pa | 3.16mm H2O |
2Pa | 0.20mm H2O | 17Pa | 1.73mm H2O | 32Pa | 3.26mm H2O |
3Pa | 0.31mm H2O | 18Pa | 1.84mm H2O | 33Pa | 3.37mm H2O |
4Pa | 0.41mm H2O | 19Pa | 1.94mm H2O | 34Pa | 3.47mm H2O |
5Pa | 0.51mm H2O | 20Pa | 2.04mm H2O | 35Pa | 3.57mm H2O |
6Pa | 0.61mm H2O | 21Pa | 2.14mm H2O | 36Pa | 3.67mm H2O |
7Pa | 0.71mm H2O | 22Pa | 2.24mm H2O | 37Pa | 3.77mm H2O |
8Pa | 0.82mm H2O | 23Pa | 2.35mm H2O | 38Pa | 3.87mm H2O |
9Pa | 0.92mm H2O | 24Pa | 2.45mm H2O | 39Pa | 3.98mm H2O |
10Pa | 1.02mm H2O | 25Pa | 2.55mm H2O | 40Pa | 4.08mm H2O |
11Pa | 1.12mm H2O | 26Pa | 2.65mm H2O | 41Pa | 4.18mm H2O |
12Pa | 1.22mm H2O | 27Pa | 2.75mm H2O | 42Pa | 4.28mm H2O |
13Pa | 1.33mm H2O | 28Pa | 2.86mm H2O | 43Pa | 4.38mm H2O |
14Pa | 1.43mm H2O | 29Pa | 2.96mm H2O | 44Pa | 4.49mm H2O |
15Pa | 1.53mm H2O | 30Pa | 3.06mm H2O | 45Pa | 4.59mm H2O |
68. What is the difference between disintegration and dissolution?
Disintegration is a process of breaking down of granules into small fragments.
Dissolution is the process in which a substance goes into a solution. It is a measure of bioavailability and therapeutic effectiveness. Dissolution is also called drug release.
69. What is the purpose of maintaining pressure gradients between processing areas and service corridors?
Pressure gradients are maintained to avoid cross contamination of products through air.
70. In oral solid manufacturing facility ‘positive’ pressure is maintained in processing area or in service corridors?
Positive pressure is maintained in service corridors with respect to processing rooms.
71. What should be the characteristic of Finger Bags used for Fluid Bed Dryer (FBD) or Fluid Bed Processor (FBP)?
Antistatic
Waterproof cloth
Able to handle granulation of highly viscous materials, such as extract powder
Non-stick cloth bag
Good permeability
Good boiling effect
Cost-efficient and durable
72. What is generally used material of construction of Finger Bags used for Fluid Bed Dryer (FBD) or Fluid Bed Processor (FBP)
Finger bags are constructed by a combination of Antistatic polymer, Nylon fabric and Cotton fabric. Following materials are also used for Finger bags’ construction.
Antistatic
Epitropic
Polypropylene
Polyester
Stain
73. What are the typically seen micron ratings of Finger Bags used for Fluid Bed Dryer (FBD) or Fluid Bed Processor (FBP)?
Micron Rating: 1, 5, 10, 15, 25, 50, 100
74. What is the formula for calculating friability test results?
Friability (%) = Weight 1 – Weight 2 / Weight 1 X 100
Where,
Weight 1 = Weight of Tablets (Initial / Before Tumbling) & Weight 2 = Weight of Tablets (After Tumbling or friability)
75. What is the limit of friability test results?
Limit: Friability (%) = Not More Than 1.0 %
76. What is Rheology?
Rheology (Greek words rheos meaning flow and logos meaning science) is the study of the flow under the influence of stress. The principle can be applied to solids, liquids, and gases.
77. Explain the types of excipients.
Organoleptic
o Color
o Flavor
o Sweetener
Stabilizers
o Preservative
o Antioxidant
o Emulsifier
o Suspending Agent
Dose Accuracy
o Diluent
o Bulking agent
o Filler
Process Aids
o Binder
o Lubricant
o Glidant
o Anti-adherent
Drug release
o Disintigrant
o Penetration enhancer
o Coating agent
78 What are the types of tablets? Or Classification of Tablets.
Classification of tablets by route of administration
Oral tablets for ingestion
Implantation tablets
Chewable tablets
Tablets used in the oral cavity
Buccal and sublingual tablets
Dental cones
Vaginal tablets
Tablets used to prepare solutions
Effervescent tablets
Dispensing tablets (DT)
Hypodermic tablets (HT)
Tablet triturates (TT)
Troches and lozenges
Classification of tablets by manufacturing process
Compressed tablets
Layered tablets
Sugar coated tablets
Film-coated tablets
Classification of tablets by onset of action
Immediate release tablets
Repeat-action tablets
Delayed-action and enteric coated tablets Controlled release tablets
79. What are the various types of tablets?
Following are various types of tablets.
- Compressed Tablet (CT)
- Sugar-Coated Tablets (SCT)
- Film-Coated Tablets (FCT)
- Enteric-Coated Tablets (ECT)
- Multiple Compressed Tablets (MCT)
- Layered Tablets
- Press-Coated Tablets
- Controlled-Release Tablets (CRT)
- Tablets for Solution (CTS)
- Effervescent Tablets
- Compressed Suppositories or Inserts
- Buccal and Sublingual Tablets
- Molded Tablets or Tablet Triturates (TT)
- Dispensing Tablets (DT)
- Hypodermic Tablets (BT)
- Compressed Tablets (CT)
80. What are the ingredients used to formulate or manufacture the various types of tablets?
Following are ingredients used to formulate or manufacture the various types of tablets.
- Active pharmaceutical ingredient
- Diluents
- Binders
- Lubricants
- Glidants
- Disintegrants
- Coloring Agents
- Flavoring Agents
81. Explain parts of the compression machine.
- Machine Hopper
- Feeder System (force feeder/ gravity feeder)
- Feeder housing
- Feed pedals
- Punches System
- Upper punch system
- Lower punch system
- Die System
- Turret
- Machine Cam Tracks
- Powder Filling Station and Weight Control
- Compression Rollers (Pre-compression, main-compression)
- Tablet Press Ejection Cam
- Take –off blade
- Discharge Chute
- Touch Screen Control Panel (HMI/ MMI)
- Electric Motors, Gears and Belts
- Lubrication Systems
82. What are the types of tablet press or compression machines?
Broadly, we there are two main types of tableting machines:
- Single-station tablet press or compression
- Multi-station tablet press or compression
- Single rotary machine
- Double rotary machine
83. What are the types of tablet Coating Machines available in the market?
• Standard Coating Pan
• Perforated Coating Pan
• Fluidized Bed Coater
84. What are the advantages of the tablet coating process?
Following are the advantages of tablet coating:
• It enhances its appearance
• Easy to consume
• Minimizes the unpleasant colour, odour or taste of drug
• Identification
• Helps to reduces drug degradation by protecting it from environmental factors
• Facilitates the packing process
• Functional coating gives functional advantages like extended release, enteric release, prolonged release etc.
85. What are the disadvantages of the tablet coating process?
Following are the disadvantages of tablet coating:
• Cost of operation, resources and material
• Equipment operation and maintenance cost
• May change tablet properties
• Residual solvent toxicity
• Waiting time between processes
• Increase process lead time
• Increase analysis load
86. Explain parts of tablet coating equipment or machine.
Following are the parts of tablet coating equipment or machine
• Perforated coating pan
• Baffles in coating pan
• Spray gun
• Spray pump e.g. Peristalsis pump, Diaphragm pump
• Electric Motors
• Air Handling unit for inlet air
o Inlet air blower
o Air Handling unit housing
o Primary filter (Washable)
o High temperature HEPA filter
o Inlet air temperature sensor
o Differential air pressure sensors across the above filters
• Ducting to supply air and exhaust air
• Control panel with PLC Control and HMI
• Exhaust air blower
• Dust collector or air Scrubber (Wet or Dry)
• Solution preparation tank
87. Explain parts of Fluid bed dryer and Fluid bed processor?
Following are the parts of Fluid bed dryer and Fluid bed equipment
• Plenum
• Product Container with PU wheel trolley
• Inflatable gasket for connection between plenum and Product Container, and Product Container and expansion chamber
• Product temperature sensor
• Inlet air temperature and RH sensor
• Damper for inlet air
• Sample collection port in Product Container
• Glass view in Product Container
• Silicon molded Dutch Woven sieves
• Conidur mesh for mechanism of vortex formation
• Expansion chamber
• Glass view in Expansion chamber
• Finger bag
• Finger bag mounting assembly
• Finger bag shaking assembly
• Inflatable gasket to seal finger bag assembly
• Broken Bag Detector (BBD) sensor OR Solid Flow Monitor (SFM) sensor
• Exhaust blower
• Exhaust filters (10 and 3 µm porosity)
• Explosion flap and Explosion port
• Inlet Air Handling Unit
o Air Handling unit housing
o Primary filter (Washable)
o High temperature HEPA filter
o Dew point sensor
o Differential air pressure sensors across the above filters
o Damper
• CFM or Air flow sensor
• Inlet air duct
• Clean in place system
• Differential pressure sensors, across filters, across finger bag, across product container
• Exhaust air temperature
• Spraying system (for top spray granulation)
88. What is a Tablet Deduster?
Deduster is an equipment used in the pharmaceutical and nutraceutical industry to remove surface dust from the tablets.
89. What are different types of tablet Deduster?
- Rotary Vibrating Deduster
- Uphill Deduster
- Brush Type Deduster
- Horizontal Deduster
- Vertical Deduster
i. Vertical Downward Conveying Deduster
ii. Vertical Upward Conveying Deduster
90. Explain in detail about different types of Tablet Deduster.
There are different types of tablet dedusters. Each has its advantages and disadvantages.
a. Rotary Vibrating Tablet Deduster
Rotary Vibrating Tablet Deduster depends on rotation and vibration principles.
It has a vibrated helical path with a perforated sieve. As the tablets vibrate and spin along the helical path with a perforated plate, burrs and dust are wiped from their surface. A dust extraction mechanism extracts the dust and the tablets drop into the collection container.
b. Uphill Tablet Deduster
Uphill tablet Dedusting machine depends on the vibration that removes burr and dust as it elevates the tablets. The deduster elevates and dedusts concurrently.
c. Brush Type Tablet Deduster
It consists of a helically wound brush installed within a stainless steel tube (same as screw conveyor) steered by an adjustable speed motor.
The brush pushes the tablets across the tube till they get to the discharge of the deduster at the top or end.
d. Horizontal Tablet Deduster
These types of tablet dedusters use perforated tubes or perforated stainless steel plates that vibrate from one side to another. It is horizontal but slants downwards that the tablets fall as the vibration conveys them over a distance of around 1 meter.
e. Vertical Tablet Deduster
Vertical tablet dedusters are of two types, Downward Conveying Tablet Dedusters and Upward Conveying Tablet Dedusters. The working principle of both types of dedusters are similar.
The dedusters rely on spiral punctured trays on an anchored central column.
91. Which Material is used to make Tablet Dedusters?
Stainless Steel: Stainless steel forms the largest portion of tablet dedusters.
Acrylic: To make the windows.
92. Which Quality Standards should a Tablet Deduster Comply with?
a. Current good manufacturing practices (cGMP) quality standards
b. ISO certification quality standards
c. CCC compliant
d. CE certification
93. How do you select the tablet deduster?
a. Height of compression machine and containers
b. Tablet Size
c. Output
d. Tablet Hardness and Features of Dust
e. Inclusion of Extra Components such as metal detector
94. Explain parts of multimill?
Material Charging Hopper: To load the material to be milled
Milling chamber: Milling of material happens within the chamber with the help of Cutting blades and desired size of particles are passed through specific size screen
Discharge port: Milled material is discharged from this part
Castor wheels: To move the mill from one place to another place
Operating Panel: To operate the equipment
Screen: To produce desired particle size
Cutting blades: To mill the material
95. What is the Material Of Construction (MOC) of multimill parts?
Product contact parts are made up of SS 316 or SS316L
Non-product contact parts are made up of SS 304 Castor wheels are made up of Polyurethane
96. What is the mechanism of size reduction when using multimill?
a. Impact Milling: Particles are reduced in size by high-speed mechanical impact or impact with other particles; also known as milling, pulverizing, or comminuting.
b. Cutting: Particles are reduced in size by mechanical shearing.
c. Screening: Particles are reduced in size by mechanically induced attrition through a screen. This process commonly is referred to as milling or deagglomeration.
97. What are the typical speeds of multimill?
Fast speed: 2880
Medium fast speed: 2160
Medium speed: 1440
Low speed: 720
Note: Nowadays multimill are available with variable frequency drive where speed can be set as per the requirement (Custom speed).
98. What are the typical settings for milling operation using multimill?
Blade direction: Impact forward or Knife forward
Machine speed: Using V belt adjustment or using VFD as per machine design
99. What is Vibro sifter?
Vibro sifter is equipment used for separating particles based upon particle size alone and without any significant particle size reduction. This process commonly is referred to as screening or bolting. Vibration and Gyratory motion plays an important role to facilitate the screening process.
100. What is the principle of Vibro sifter?
Vibro sifters work on the principle of separation. Particles are segregated based upon particle size alone and without any significant particle size reduction. This process commonly is referred to as screening or bolting. Vibration and Gyratory motion plays an important role to facilitate the screening process.
The mechanism on which Vibro Sifter works is the principle of gyratory vibrations. The material is separated based on its particle size. Once the motor gets energized, vibration is caused in the screen/. This makes material travel across the sieves according to its particle size and sieve/ screen size.
Separator subclasses as per SUPAC: Vibratory/ Shaker and Centrifugal.
101. What is the gyratory motion of a vibro sifter and how does it get generated?
In the vibro sifter gyratory motion is obtained from a specially designed gyro motor, which is fitted underneath the vibrating assembly. A specially designed rugged spring completely isolates this assembly from the base with the help of Gyro-motor.

The motor is fitted with eccentric weights present at its top as well as base to create centrifugal force. This whole assembly is covered by an SS plate.
102. What are other names of vibro sifters?
The vibro sifter machine is also known as:
Vibro Screen
Vibrating Screen
Lab Vibro Sifter
Pharmaceutical Sifter
Vibro Sieve
Vibro Sifter Machine
Powder Sieving Machine
103. What are the salient features or use of vibro sifter?
• Gradation and separation of dry powder, granules, semi solids and liquids
• Main functioning mechanical arrangement is suspended on a spring to prevent vibration on the floor
• Easy assembling and disabling
• Easy to clean
104. What are different parts of vibro sifter?
• Dust cover
• Clamp for assembling of different parts
• Inlet
• Sieve/ screen
• Vibrating motor for Gyratory motion with eccentrically arranged top and bottom hammer
• Caster wheel
• Discharge port
• Spring
105. How to discharge the static electricity which may get generated over the vibro sifter sieve when silicone bonded sieve is used?
Following are the solutions to discharge the static electricity which may get generated over the vibro sifter sieve when silicone bonded screen is used:
i. Using antistatic screen
ii. Use C clamp over the silicone bonded sieve which makes the entire assembly conductive and to provide earthing to the body of the equipment.
106. What is a solution preparation vessel?
The solution preparation vessel is a closed tank used to prepare solution at room temperature or elevated temperature by using electrical heating or steam heating. To mix the solution homogeneously, it consists of stirring to create a vortex inside the solution.
107. What is the use of solution preparation vessels in the pharmaceutical industry?
The solution preparation vessel is used to prepare various types of solutions such as binder solution, coating solution, heating of water, liquid preparations such as syrup, suspension, solutions, etc. The vessel is used to ensure a homogeneous mix.
108. Explain parts of solution preparation vessel and Material of Construction (MOC)?
• Tank – SS316 or SS316L
• Stirrer – SS316 or SS316L
• Thermal Insulation
• Motor
• Variable Frequency Drive
• Control Panel
• Pressure gauge for jacket
• Temperature sensor – Product contact part SS316 or SS316 L
• Discharge valve (Zero dead leg and sanitary type)(Note: Ball valve is not acceptable) – SS316 or SS316L
• Caster wheel for movement (Need based) – Polyurethane
109. What is vortex and how is it helpful for solution preparation?
A circular, spiral, or helical motion in a fluid. A vortex often forms around areas of low pressure and attracts the fluid (and the objects moving within it) toward its center.
Velocity in the vortex is maximum next to the axis and inversely decreases with the radius.
Vortex enhances the desired solubility of pharmaceutical binder solute into the various solvents.

110. What should be characteristics of the solution preparation vessel?
• Zero dead leg and sanitary design components
• Stationary or mobile use
• Capable to handle wide temperature range (design as per requirement)
• The Internal surfaces of our preparation vessels are flush ground and mirror polished to <0.3 Microns Ra and electro-polished
• Easy to clean
• Adjustable speed of stirrer
• Adjustable temperature
• 21 CFR Part 11 compliant and EU Annex 11 Compliant
• Low maintenance and long service
111. What are the different particle size reduction mechanisms?
Particle size reduction mechanisms | Description |
Impact | Particle size reduction by applying an instantaneous force perpendicular to the particle/ agglomerate surface. The force can result from particle-to-particle or particle-to-mill surface collision. |
Attrition | Particle size reduction by applying a force in a direction parallel to the particle surface. |
Compression | Particle size reduction by applying a force slowly (as compared to Impact) to the particle surface in a direction toward the center of the particle. |
Cutting | Particle size reduction by applying a shearing force to a material. |
112. What are the types of Equipment used for Particle Size Reduction/ Separation. Explain its Operating Principles.
Types of Equipment | Operating Principles |
Fluid Energy Milling | Particles are reduced in size as a result of high-speed particle-to-particle impact and/or attrition; also known as micronizing. |
Impact Milling | Particles are reduced in size by high-speed mechanical impact or impact with other particles; also known as milling, pulverizing, or comminuting. |
Cutting | Particles are reduced in size by mechanical shearing. |
Compression Milling | Particles are reduced in size by compression stress and shear between two surfaces. |
Screening | Particles are reduced in size by mechanically induced attrition through a screen. This process commonly is referred to as milling or deagglomeration. |
Tumble Milling | Particles are reduced in size by attrition utilizing grinding media. |
Separating | Particles are segregated based upon particle size alone and without any significant particle size reduction. This process commonly is referred to as screening or bolting. |
113. Explain Equipment Classifications for Particle Size Reduction/ Separation. Give examples of Equipment for each classification.
Equipment type | Sub classification description | Sub classification |
Fluid Energy Mills | Fluid energy mill subclasses have no moving parts and primarily are distinguished from one another by the configuration and/ or shape of their chambers, nozzles, and classifiers. | Tangential Jet Loop/ Oval Opposed Jet Opposed Jet with Dynamic Classifier Fluidized Bed Fixed Target Moving Target High Pressure Homogenizer E.g. Jet mill |
Impact Mills | Impact mill subclasses primarily are distinguished from one another by the configuration of the grinding heads, chamber grinding liners (if any), and classifiers. | Hammer Air Swept Hammer Conventional Pin/ Disc Cage E.g. Hammer millPin mill Impact millCage millDisk millBall mill |
Cutting Mills | Although cutting mills may differ from one another in whether the knives are movable or fixed and in the classifier configuration, no cutting mill subclasses have been identified. | No sub class E.g. MultimillComill |
Compression Mills | Although compression mills may differ from one another in whether one or both surfaces are moving, no compression mill subclasses have been identified. | No sub class E.g. Roller mill |
Screening Mills | Screening mill subclasses primarily are distinguished from one another by the rotating element. | Rotating Impeller Rotating Screen Oscillating Bar E.g. MultimillComill |
Tumbling Mills | Tumbling mill subclasses primarily are distinguished from one another by the grinding media used and by whether the mill is vibrated. | Ball Media Rod Media Vibrating E.g. Ball millTubular Rod Mills |
Separators | Separator subclasses primarily are distinguished from one another by the mechanical means used to induce particle movement. | Vibratory/ Shaker Centrifugal E.g. Vibro sifterUltra Centrifugal Mill |
Source: fda.gov
114. What is Blending and Mixing?
Blending and Mixing is the process of reorientation of particles relative to one another in order to achieve uniformity.
115. What are the Operating Principles of different equipment for Blending and Mixing?
Types of Equipment | Operating Principles |
Diffusion Blending (Tumble blending) | Particles are reoriented in relation to one another when they are placed in random motion and interparticular friction is reduced as the result of bed expansion (usually within a rotating container). |
Convection Mixing (also known as paddle or plow mixing) | Particles are reoriented in relation to one another as a result of mechanical movement. |
Pneumatic Mixing | Particles are reoriented in relation to one another as a result of the expansion of a powder bed by gas. |
116. Equipment Classifications used for Blending and Mixing
Equipment type | Sub classification description | Sub classification |
Diffusion Mixers (Tumble) | Diffusion mixer subclasses primarily are distinguished by geometric shape and the positioning of the axis of rotation. | • V-blenders• Double Cone Blenders• Slant Cone Blenders• Cube Blenders• Bin Blenders• Horizontal/ Vertical/ Drum Blenders• Static Continuous Blenders• Dynamic Continuous Blenders |
Convection Mixers | Convection blender subclasses primarily are distinguished by vessel shape and impeller geometry. | • Ribbon Blenders• Orbiting Screw Blenders• Planetary Blenders• Forberg Blenders• Horizontal Double Arm Blenders• Horizontal High Intensity Mixers• Vertical High Intensity Mixers• Diffusion Mixers (Tumble) with Intensifier/Agitator |
Pneumatic Mixers | Although pneumatic mixers may differ from one another in vessel geometry, air nozzle type, and air nozzle configuration, no pneumatic mixer subclasses have been identified. | No sub lass |
Source: fda.gov
117. What is Granulation
Granulation is the process of creating granules. The powder morphology is modified through the use of either a liquid that causes particles to bind through capillary forces or dry compaction forces.
The process will result in one or more of the following powder properties:
Enhanced flow;
Increased compressibility;
Densification;
Alteration of physical appearance to more spherical, uniform, or larger particles;
And/or enhanced hydrophilic surface properties.
118. What are the Operating Principles of different Granulation?
Types of Granulation | Operating Principles |
Dry Granulation | Dry powder densification and/or agglomeration by direct physical compaction. |
Wet High-Shear Granulation | Powder densification and/or agglomeration by the incorporation of a granulation fluid into the powder with high-power-per-unit mass, through rotating high-shear forces. |
Wet Low-Shear Granulation | Powder densification and/or agglomeration by the incorporation of a granulation fluid into the powder with low-power-per-unit mass, through rotating low-shear forces. |
Low-Shear Tumble Granulation | Powder densification and/or agglomeration by the incorporation of a granulation fluid into the powder with low-power-per-unit mass, through rotation of the container vessel and/or intensifier bar. |
Extrusion Granulation | Plasticization of solids or wetted mass of solids and granulation fluid with linear shear through a sized orifice using a pressure gradient. |
Rotary Granulation | Spheronization, agglomeration, and/or densification of a wetted or non-wetted powder or extruded material. This is accomplished by centrifugal or rotational forces from a central rotating disk, rotating walls, or both. The process may include the incorporation and/or drying of a granulation fluid. |
Fluid Bed Granulation | Powder densification and/or agglomeration with little or no shear by direct granulation fluid atomization and impingement on solids, while suspended by a controlled gas stream, with simultaneous drying. |
Spray Dry Granulation | A pumpable granulating liquid containing solids (in solution or suspension) is atomized in a drying chamber and rapidly dried by a controlled gas stream, producing a dry powder. |
Hot-melt Granulation | An agglomeration process that utilizes a molten liquid as a binder(s) or granulation matrix in which the active pharmaceutical ingredient (API) is mixed and then cooled down followed by milling into powder. This is usually accomplished in a temperature controlled jacketed high shear granulating tank or using a heated nozzle that sprays the molten binders(s) onto the fluidizing bed of the API and other inactive ingredients. |
Melt Extrusion | A process that involves melting and mixing API and an excipient (generally a polymer) using low or high shear kneading screws followed by cooling and then milling into granules. Thermal energy for melting is usually supplied by the electric/water heater placed on the barrel. Materials are either premixed or fed into an extruder separately. Melt extruder subclasses primarily are distinguished by the configuration of the screw. • Single screw extruder • Twin screw extruder |
119. Equipment Classifications used for granulation.
Equipment type | Sub classification description | Sub classification |
Dry Granulator | Dry granulator subclasses primarily are distinguished by the densification force application mechanism. | • Slugging • Roller Compaction |
Wet High-Shear Granulator | Wet high-shear granulator subclasses primarily are distinguished by the geometric positioning of the primary impellers; impellers can be top, bottom, or side driven. | • Vertical (Top or Bottom Driven) • Horizontal (Side Driven) |
Wet Low-Shear Granulator | Wet low-shear granulator subclasses primarily are distinguished by the geometry and design of the shear inducing components; shear can be induced by rotating impeller, reciprocal kneading action, or convection screw action. | • Planetary • Kneading • Screw |
Low-Shear Tumble Granulator | Although low-shear tumble granulators may differ from one another in vessel geometry and type of dispersion or intensifier bar, no low-shear tumble granulator subclasses have been identified. | • Slant cone • Double cone • V-blender |
Extrusion Granulator | Extrusion granulator subclasses primarily are distinguished by the orientation of extrusion surfaces and driving pressure production mechanism. | • Radial or Basket • Axial • Ram • Roller, Gear, or Pelletizer |
Rotary Granulator | Rotary granulator subclasses primarily are distinguished by their structural architecture. They have either open top architecture, such as a vertical centrifugal spheronizer, or closed top architecture, such as a closed top fluid bed dryer. | • Open • Closed |
Fluid Bed Granulator | Although fluid bed granulators may differ from one another in geometry, operating pressures, and other conditions, no fluid bed granulator subclasses have been identified. | No subclass |
Spray Dry Granulator | Although spray dry granulators may differ from one another in geometry, operating pressures, and other conditions, no spray dry granulator subclasses have been identified. | No subclass |
Hot-melt Granulator | Although, hot-melt granulator may differ from one another in primarily melting the 455 inactive ingredient (particularly the binder or other polymeric matrices), no 456 subclasses have been identified at this time. | No subclass |
120. What is an integrated unit as per SUPAC?
When a single piece of equipment is capable of performing multiple discrete unit operations (i.e. mixing, granulating, drying), the unit was evaluated solely for its ability to granulate. If multifunctional units were incapable of discrete steps (fluid bed granulator/ drier), the unit was evaluated as an integrated unit.
Source: fda.gov
121. What is Drying?
The removal of a liquid from a solid by evaporation.
122. What are the Operating Principles of different equipment for Drying?
Types of Drying principle | Details of Principles |
Direct Heating, Static Solids Bed | Heat transfer is accomplished by direct contact between the wet solids and hot gases. The vaporized liquid is carried away by the drying gases. There is no relative motion among solid particles. The solids bed exists as a dense bed, with the particles resting upon one another. |
Direct Heating, Moving Solids Bed | Heat transfer is accomplished by direct contact between the wet solids and hot gases. The vaporized liquid is carried away by the drying gases. Solids motion is achieved by either mechanical agitation or gravity force, which slightly expands the bed enough to flow one particle over another. |
Direct Heating, Fluidized Solids Bed | Heat transfer is accomplished by direct contact between the wet solids and hot gases. The vaporized liquid is carried away by the drying gases. The solids are in an expanded condition, with the particles supported by drag forces caused by the gas phase. The solids and gases intermix and behave like a boiling liquid. This process commonly is referred to as fluid bed drying. |
Direct Heating, Dilute Solids Bed, Spray Drying | Heat transfer is accomplished by direct contact between a highly dispersed liquid and hot gases. The feed liquid may be a solution, slurry, emulsion, gel or paste, provided it is pumpable and capable of being atomized. The fluid is dispersed as fine droplets into a moving stream of hot gases, where they evaporate rapidly before reaching the wall of the drying chamber. The vaporized liquid is carried away by the drying gases. The solids are fully expanded and so widely separated that they exert essentially no influence on one another. |
Direct Heating, Dilute Solids Bed, Flash Drying | Heat transfer is accomplished by direct contact between wet solids and hot gases. The solid mass is suspended in a finely divided state in a high-velocity and high-temperature gas stream. The vaporized liquid is carried away by the drying gases. |
Indirect Conduction, Moving Solids Bed | Heat transfer to the wet solid is through a retaining wall. The vaporized liquid is removed independently from the heating medium. Solids motion is achieved by either mechanical agitation or gravity force, which slightly expands the bed enough to flow one particle over another. |
Indirect Conduction, Static Solids Bed | Heat transfer to the wet solid is through a retaining wall. The vaporized liquid is removed independently from the heating medium. There is no relative motion among solid particles. The solid bed exists as a dense bed, with the particles resting upon one another. |
Indirect Conduction, Lyophilization | Drying in which the water vapor sublimes from the product after freezing. |
Gas Stripping | Heat transfer is a combination of direct and indirect heating. The solid motion is achieved by agitation and the bed is partially fluidized. |
Indirect Radiant, Moving Solids Bed | Heat transfer is accomplished with varying wavelengths of energy. Vaporized liquid is removed independently from the solid bed. The solid’s motion is achieved by mechanical agitation, which slightly expands the bed enough to flow one particle over one another. This process commonly is referred to as microwave drying. |
123. Equipment Classifications used for drying.
Equipment type | Sub classification description | Sub classification |
Direct Heating, Static Solids Bed | Static solids bed subclasses primarily are distinguished by the method of moving the solids into the dryer. | • Tray and Truck • Belt |
Direct Heating, Moving Solids Bed | Moving solids bed subclasses primarily are distinguished by the method or technology for moving the solid bed. | • Rotating Tray • Horizontal Vibrating Conveyor |
Direct Heating, Fluidized Solids Bed (Fluid Bed Dryer) | Although fluid bed dryers may differ from one another in geometry, operating pressures, and other conditions, no fluidized solids bed dryer subclasses have been identified. | No subclass |
Direct Heating, Dilute Solids Bed, Spray Dryer | Although spray dryers may differ from one another in geometry, operating pressures, and other conditions, no spray dryer subclasses have been identified. | No subclass |
Direct Heating, Dilute Solids Bed, Flash Dryer | Although flash dryers may differ from one another in geometry, operating pressures, and other conditions, no flash dryer subclasses have been identified. | No subclass |
Indirect Conduction Heating, Moving Solids Bed | Moving solids bed subclasses primarily are distinguished by the method or technology for moving the solids bed. | • Paddle • Rotary (Tumble) • Agitation |
Indirect Conduction Heating, Static Solids Beds | No indirect heating, static solids bed shelf dryer subclasses have been identified. | No subclass |
Indirect Conduction, Lyophilization | No lyophilizer subclasses have been identified. | No subclass |
Gas Stripping | Although gas stripping dryers may differ from one another in geometry, shape of agitator, and how fluidizing gas is moved through the bed, no gas stripping dryer subclasses have been identified. | No subclass |
Indirect Radiant Heating, Moving Solids Bed (Microwave Dryer) | Although microwave dryers may differ from one another in vessel geometry and the way microwaves are directed into the solids, no indirect radiant heating, moving solids bed dryer subclasses have been identified. | No subclass |
Source: fda.gov
124. What is Unit Dosing?
The division of a powder blend into uniform single portions for delivery to patients.
125. What are the Operating Principles of different equipment for Unit Dosing?
Types of Unit Dosing principle | Details of Principles |
Tabletting | The division of a powder blend in which compression force is applied to form a single unit dose. |
Encapsulating | The division of material into a hard gelatin capsule. Encapsulators should all have the following operating principles in common: rectification (orientation of the hard gelatin capsules), separation of capsule caps from bodies, dosing of fill material/formulation, rejoining of caps and bodies, and ejection of filled capsules. |
Powder Filling | The division of a powder blend into a container closure system. |
126. Equipment Classifications used for Unit Dosing.
Equipment type | Sub classification description | Sub classification |
Tablet Press | Tablet press subclasses primarily are distinguished from one another by the method that the powder blend is delivered to the die cavity. Tablet presses can deliver powders without mechanical assistance (gravity), with mechanical assistance (power assisted), by rotational forces (centrifugal), and in two different locations where a tablet core is formed and subsequently an outer layer of coating material is applied (compression coating). | • Gravity• Power Assisted• Centrifugal• Compression Coating |
Tablet Press | Tablet press subclasses are also distinguished from one another for some special types of tablets where more than one hopper and precise powder feeding mechanism might be necessary. | • Multi-tablet press for micro/mini tablet • Multi-layer tablet press (bi-layer, tri-layer) |
Encapsulator | Encapsulator subclasses primarily are distinguished from one another by the method that is used for introducing material into the capsule. Encapsulators can deliver materials with a rotating auger, vacuum, vibration of perforated plate, tamping into a bored disk (dosing disk), or cylindrical tubes fitted with pistons (dosator). | • Auger• Vacuum• Vibratory• Dosing Disk• Dosator |
Powder Filler | Subclasses of powder fillers primarily are distinguished by the method used to deliver the predetermined amount for container fill. | • Vacuum• Auger |
Source: fda.gov
127. What is Coating?
The uniform deposition of a layer of material on or around a solid dosage form.
128. Why is the coating done?
Coating is done for the following reasons:
a. Protect the drug from its surrounding environment (air, moisture, and light), with a view to improving stability.
b. Mask unpleasant taste, odor, or color of the drug.
c. Increase the ease of ingesting the product for the patient.
d. Impart a characteristic appearance to the tablets, which facilitates product identification and aids patient compliance.
e. Provide physical protection to facilitate handling. This includes minimizing dust generation in subsequent unit operations.
f. Reduce the risk of interaction between incompatible components. This would be achieved by coating one or more of the offending ingredients.
g. Modify the release of the drug from the dosage form. This includes delaying, extending, and sustaining drug substance release.
h. Modify the dosage form by depositing the API or drug substance on or around a core tablet, which could be a placebo core tablet or a tablet containing another drug or a fractional quantity of the same drug.
129. What are the major techniques used for coating?
The coating material deposition typically is accomplished through one of six major techniques:
a. Sugar Coating – Deposition of coating material onto the substrate from aqueous solution/suspension of coatings, based predominantly upon sucrose as a raw material.
b. Film Coating – The deposition of polymeric film onto the solid dosage form.
c. Core Enrobing – The gelatin coating of gravity or force fed pre- formed tablets or caplets.
d. Microencapsulation – The deposition of a coating material onto a particle, pellet, granule, or bead core. The substrate in this application ranges in size from submicron to several millimeters. It is this size range that differentiates it from the standard coating described in 1 and 2 above.
e. Compression Coating (also addressed in the Unit Dosing section) – A coating process where a dry coatings blend is applied on a previously compressed core tablet using a tablet compression machine.11 Therefore, this process is also known as a dry coating process that does not involve any water or any other solvent in the coating process.
f. Active/ API coating – Deposition of active pharmaceutical ingredient (API or drug substance) on or around a core tablet utilizing any of the above five coating techniques.
Source: fda.gov
130. What are the Operating Principles of different equipment for coating?
Types of coating | Details of Principles |
Pan Coating | The uniform deposition of coating material onto the surface of a solid dosage form, or component thereof, while being translated via a rotating vessel. |
Gas Suspension | The application of a coating material onto a solid dosage form, or component thereof, while being entrained in a process gas stream. Alternatively, this may be accomplished simultaneously by spraying the coating material and substrate into a process gas stream. |
Vacuum Film Coating | This technique uses a jacketed pan equipped with a baffle system. Tablets are placed into the sealed pan, an inert gas (i.e., nitrogen) is used to displace the air and then a vacuum is drawn. |
Dip Coating | Coating is applied to the substrate by dipping it into the coating material. Drying is accomplished using pan coating equipment. |
Electrostatic Coating | A strong electrostatic charge is applied to the surface of the substrate. The coating material containing oppositely charged ionic species is sprayed onto the substrate. |
Compression Coating | The division of a powder blend in which compression force is applied to form a single unit dose. |
131. Equipment Classifications used for coating.
Equipment type | Sub classification description | Sub classification |
Pan Coating | Pan coating subclasses primarily are distinguished by the pan configuration, the pan perforations, and/or the perforated device used to introduce process air for drying purposes. Perforated coating systems include both batch and continuous coating processes. | • Non-perforated (conventional) Coating System • Perforated Coating System |
Gas Suspension | Gas suspension subclasses primarily are distinguished by the method by which the coating is applied to the substrate. | • Fluidized Bed with bottom spray mechanism • Fluidized Bed with tangential spray mechanism • Fluidized Bed with top spray mechanism • Fluidized Bed with Wurster column • Spray Congealing/Drying |
Vacuum Film Coating | Although there may be differences in the jacketed pan, baffle system, or vacuum source, no vacuum film coating subclasses have been identified. | No sub class |
Dip Coating | Because of the custom design associated with this class of coating, no dip 1013 coating subclasses or examples have been identified. | No sub class |
Electrostatic Coating | Because of the custom design associated with this class of coating, no 1018 electrostatic coating subclasses or examples have been identified. | No sub class |
Compression Coating | Refer tablet press principle Unit Dosing section of previous post. | No sub class |
Source: fda.gov
132. What is Printing?
The marking of a capsule or tablet surface for the purpose of product identification.
Printing may be accomplished by either the application of a contrasting colored polymer (ink) onto the surface of a capsule or tablet, or by the use of laser etching. The method of application, provided the ink formulation is not altered, is of no consequence to the physical-chemical properties of the product.
133. What is Drilling?
The drilling or ablating of a hole or holes through the polymeric film coating shell on the surfaces of a solid oral dosage form using a laser.
The polymeric film shell is not soluble in vivo. The hole or holes allow for the modified release of the drug from the core of the dosage form.
134. What are the Operating Principles of different equipment for Printing and Drilling?
Types of Printing/ Drilling | Details of Principles |
Ink-Based Printing | The application of contrasting colored polymer (ink) onto the surface of a tablet or capsule. |
Laser Etching | The application of identifying markings onto the surface of a tablet or capsule using laser-based technology. |
Drilling | A drilling system typically is a custom built unit consisting of a material handling system to orient and hold the solid dosage form, a laser (or lasers), and optics (lenses, mirrors, deflectors, etc.) to ablate the hole or holes, and controls. The drilling unit may include debris extraction and inspection systems as well. The sorting, orienting, and holding equipment commonly is provided by dosage form printing equipment manufacturers, and is considered ancillary in this use. |
135. Equipment Classifications used for Printing and Drilling.
Equipment type | Sub classification description | Sub classification |
Ink-Based Printing | Ink-based printing subclasses primarily are distinguished by the method by which the marking is applied to a capsule or tablet surface. | • Offset • Ink Jet |
Laser Etching (Printing) | Although laser etching systems may differ from one another, no laser etching subclasses have been identified. | No sub class |
Drilling | The method of producing the laser pulse that ablates the hole(s) is of no consequence to the physical-chemical properties of the product. Therefore, no dosage form drilling equipment subclasses have been identified. | No sub class |
Source: fda.gov
136. What is excipient?
The word excipient originates from the Latin excipere, which means to receive; hence, the excipient receives the active substance.
As per European Pharmacopoeia (Ph. Eur.) “An excipient is any component, other than the active substance(s), present in a medicinal product or used in the manufacture of the product. The intended function of an excipient is to act as the carrier (vehicle or basis) or as a component of the carrier of the active substance(s) and, in so doing, to contribute to product attributes such as stability, biopharmaceutical profile, appearance and patient acceptability and to the ease with which the product can be manufactured. Usually, more than one excipient is used in the formulation of a medicinal product.”
147. What are the typical functions of excipients?
Excipients play a role in the formulation as Diluent, Binder, Disintegrant, Glidant, Lubricant, Coatings agent, or Coloring agent. It can further classified depending on its functions in the dosage form, which includes:
(i) Modulating solubility and bioavailability of the drug,
(ii) Enhancing stability of the drug in its dosage forms,
(iii) Maintaining a required polymorphic form,
(iv) Maintaining pH and osmolarity of liquid products,
(v)Antioxidants,
(vi) Preventing aggregation or dissociation agent,
(vii) Modulating the immunogenic response of drug,
(viii) Suspending agent,
(ix) Emulsifier,
(x) Aerosol propellants,
(xi) Base or tablet diluent
138. What is role of Diluents as an excipient?
Diluents are the material which provides bulk to the formulation and enable accurate dosing of potent ingredients.
139. Give a few examples of Diluents as an excipient?
Microcrystalline cellulose, Lactose, dextrin, glucose, sucrose, sorbitol, silicates, calcium and magnesium salts, sodium or potassium chloride, starch, lactose
140. What is the role of Binder as an excipient?
Binders, compression aids, granulating agents are the materials which bind the ingredients together giving form and mechanical strength and form granules for tablet, capsule or relevant formualtions
141. Give a few examples of Binder as an excipient?
Polyvinyl pyrrolidone, starch, gelatin, cellulose derivatives, sugars, sugar alcohols and cellulose derivatives
142. What is the role of Disintegrant as an excipient?
Disintegrant aid in dispersion of the tablet in the gastrointestinal tract, releasing the active ingredient and increasing the surface area for dissolution.
143. Give a few examples of Disintegrant as an excipient?
Starch, sodium starch glycollate, cross – linked polyvinyl pyrrolidone super disintegrants, cellulose derivatives and alginates, and crospovidone.
144. What is role of Glidant as an excipient?
Glidant improves the flow of powders during tablet manufacturing by reducing friction and adhesion between particles. It also used as anti-caking agents.
145. Give a few examples of Glidant as an excipient?
Colloidal anhydrous silicon and other silica compounds, talc, magnesium stearate
146. What is the role of Lubricant as an excipient?
Lubricants are used to prevent sticking of granules from die and punch wall during compression.
147. Give a few examples of Lubricant as an excipient?
Stearic acid and its salts (e.g. magnesium stearate), polyethylene glycol, sodium chloride
148. What is the role of coating agents as an excipient?
Coating agents have various functions such as, protect tablets from the environment (air, light and moisture), increase the mechanical strength, mask taste and smell, aid swallowing, assist in product identification.
It also can be used to modify release of the active ingredient.
149. Give a few examples of coating agents as an excipient?
Sugar, cellulose acetate phthalate etc.
150. What is the role of Colouring agent as an excipient?
Coloring agents improves acceptability to patients, aids identification and prevents counterfeiting. It also increases the stability of light-sensitive drugs.
151. Give a few examples of Colouring agents as an excipient?
Iron oxide, natural pigments, and other synthetic dyes.
152. Explain excipient classification based on objective of addition in dosage form.
Type of excipient | Objective in dosage form |
Improve organoleptic property | Color Flavor Sweetener Masking of unpleasant test |
Stabilizers | Preservative Antioxidant Emulsifier Suspending agent Isotonicity agent Maintaining pH and osmolarity |
Dosage accuracy | Diluent Filler Bulking agent |
Process aids | Binder Glidant Lubricant Anti-adherent |
Drug release | Disintigrant Permiability enhancer Release rate limiting agent |
153. What is immediate – release dosage form?
This is the dosage form intended to release the drug immediately after administration.
154. What is Delayed – release dosage form?
This is the dosage form where drug is not released until a physical event has occurred, e.g., change in pH etc.
155. What is sustained – release dosage form?
This is the dosage form where drug is released slowly over extended time.
156. What is a soluble tablet?
Soluble tablets are those which dissolve in water before administration.
157. What is a Dispersible tablet?
Tablet is added to water to form a suspension to administer.
158. What is an Effervescent tablet?
Tablet which is added into water. Tablet releases carbon dioxide to form an effervescent solution.
159. What is a Chewable tablet?
To administer the dose, the tablet is chewed and swallowed.
160. What is Chewable gum?
The formulation is chewed and removed from the mouth after a directed time as per the label claim.
161. What are Buccal and sublingual tablets?
The tablet which is placed in the oral cavity for local or systemic action is called Buccal and sublingual.
162. What is an Orally disintegrating tablet?
The tablet which gets dissolved or disintegrated in the mouth without the need for water is called an orally disintegrating tablet.
163. What is Lozenge?
Lozenge is a slowly dissolving tablet designed to be sucked in the mouth.
164. What is Pastille?
Pastille is the tablet consisting of gelatin and glycerine that facilitate dissolving tablets slowly in the mouth.
165. What is a Hard gelatin capsule?
Hard gelatin capsule is a two piece capsule shell that is filled with powder, granulate, tablets, semisolid or liquid in it.
166. What is Soft gelatin capsule (softgel)?
Soft gelatin capsule is a one piece capsule that contains a liquid or semisolid filled in it.
References:
1. WHO GMP Guidelines: Guide to Master Formulae, WHO/FWC/IVB/QSS/VQR, 2011
EU and PIC GMP guidelines: EudraLex Volume 4, Chapter 4: Documentation
PIC/S guidelines: Chapter 4: Documentation
Health Canada GMP guidelines: Good manufacturing practices guide for drug products (GUI-0001), Manufacturing control, C.02.011
U.S. FDA: CFR 21, Chapter I, Subchapter F: Biologics, Part 211 Current Good Manufacturing Practice for Finished Pharmaceuticals; Subpart F–Production and Process Controls, Sec. 211.100 Written procedures; deviations; and Subpart J–Records and Reports; Sec. 211.186 Master production and control records
U.S. FDA: CFR 21, Chapter I, Subchapter F: Biologics; Subchapter C: Drugs General; Part 211 Current Good Manufacturing Practice for Finished Pharmaceuticals; Subpart J– Records and Reports; Sec. 211.188 Batch production and control records.
India: The drugs and cosmetics act, 1940 and The drugs and cosmetics rules, 1945, Schedule M, 12. Documentation and records]
2. PART 314 — APPLICATIONS FOR FDA APPROVAL TO MARKET A NEW DRUG, Subpart A – General Provisions Sec. 314.3 Definitions.
3. 21 CFR PART 210: CURRENT GOOD MANUFACTURING PRACTICE IN MANUFACTURING, PROCESSING, PACKING, OR HOLDING OF DRUGS; GENERAL Sec. 210.1 Status of current good manufacturing practice regulations.
5. Wet Granulation:
End-Point Determination and Scale-Up, By Michael Levin, Ph. D., Metropolitan Computing Corporation East Hanover, New Jersey, USA
6. Saudi Pharmaceutical Journal
Volume 20, Issue 1, January 2012, Pages 9-19, Saudi Pharmaceutical Journal, Review article, Upgrading wet granulation monitoring from hand squeeze test to mixing torque rheometry Author links open overlay panel Walid F. Sakr Mohamed A. Ibrahim Fars K. Alanazi Adel A. Sakr
7. natoli.com
8. pacifictools.in