Standard Operating Procedure for Laboratory Instrument Maintenance
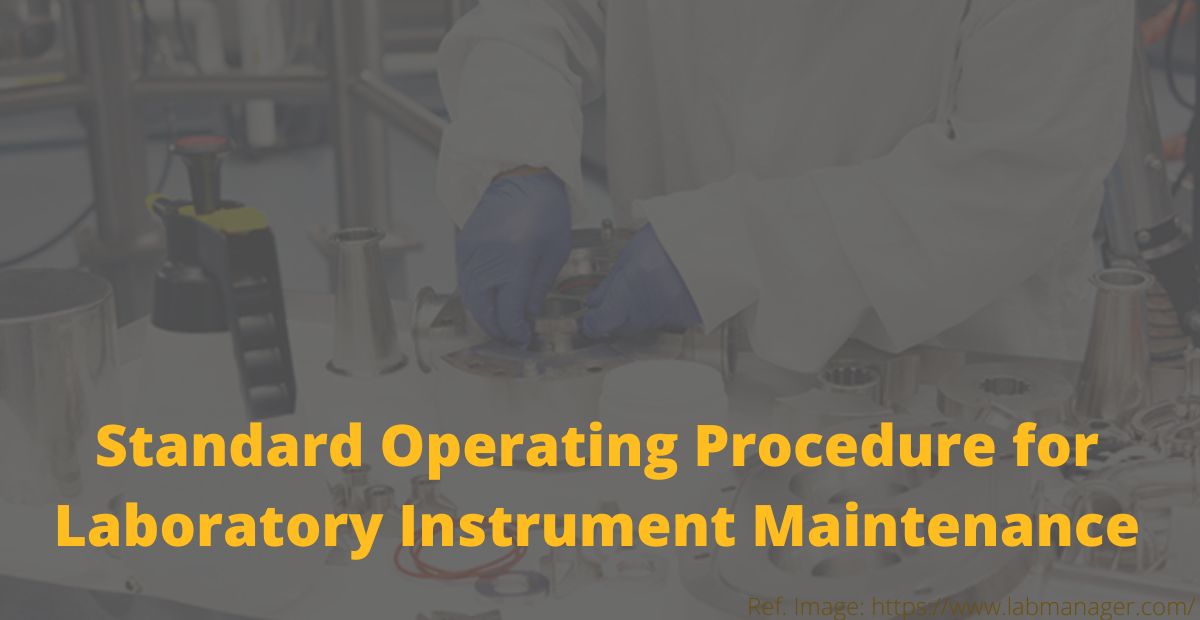
Standard Operating Procedure for Laboratory Instrument Maintenance
1. Purpose:
To lay down a procedure for Laboratory instrument maintenance.
2. Scope
The scope of this is applicable Laboratory instrument maintenance in the pharmaceutical quality control laboratory at [company name].
3. Responsibility
Quality control person: To perform cleaning and maintenance of instrument as per as per SOP
Quality control supervisor: To verify the cleaning and maintenance of instrument
Head Quality control: Effective implementation of SOP
4. Definitions
Not Applicable
5. Procedure
5.1 General instructions for laboratory maintenance
• The key to maintain the laboratory instrument is to operate the instrument as per procedure and regular cleaning after operation as per procedure.
• Analyst should follow the Good Laboratory Practices while performing analysis and handling instruments.
• While performing the analysis and during handling of Hazardous and Toxic Chemicals use Personal Protective Equipment (PPE) such as Hand Gloves required for handling respective chemicals (Acid, Alkali, Heat – Resistant, Surgical, Pure Latex and Cotton Gloves etc.), Safety Goggles and Nose Mask (wherever required).
• Record the details of instrument usage in the Instrument Usage Logbook as applicable.
• Troubleshooting of instrument shall be done as per respective instrument procedure.
• Dos, Don’ts, instructions, and pictorials are displayed in the laboratory. Follow the guidance provided in the Dos, Don’ts, instructions, and pictorials.
• Dos, Don’ts, instructions, and pictorials shall be prepared using the approved template which is governed through SOP.
• While performing the analysis on the instruments, if any abnormality observed, inform to the supervisor immediately. Follow the applicable procedure to troubleshoot. In case the troubleshooting does not work, take help of service engineer for the rectification.
• When instrument is under the maintenance, it shall be labeled as “Instrument under maintenance”. The label shall be signed by QC person and verified by supervisor.
• Service Engineer can be called telephonically or through e-mail.
• In case any instrument breakdown needs to be handled by company engineering department, it shall be intimated to engineering department using maintenance request form.
• Laboratory cleaning should be done on regular basis as per respective SOP and as per defined frequency.
• Preventive maintenance of the instrument shall be done as per schedule which is governed as per respective procedure.
• Breakdown maintenance trend shall be done to understand which instrument is triggering repeated maintenance and need based; it shall be serviced comprehensively to prevent the repeated maintenance.
5.2 Maintenance of High Performance Liquid Chromatography (HPLC):
5.2.1 Cleaning of HPLC inline filter:
• Place the inline filter in the Hot Water for 30 to 35 minutes
• Then place the inline filter in to syndicator and sonicate it in methanol for 15 minutes
• Above inline filter cleaning shall be followed on monthly basis.
• Record the details of inline filter cleaning in the respective filter cleaning record.
5.2.1 Cleaning of HPLC suction filter:
• Sonicate the suction filters in dilute Nitric acid (14.3 ml acid in 100 ml water) for 10 minutes.
• Deep the filter in boiling water for 5 – 7 minutes.
• Sonicate the filter in the Isopropyl alcohol for 10 – 12 minutes.
• Then sonicate the filter in the Methanol for 10 – 12 minutes.
• Finally, sonicate the filter in the ambient water for 10 minutes.
• Record the cleaning in the respective format for cleaning of suction filter of HPLC.
• Above inline filter cleaning shall be followed on monthly basis.
6. Frequency
• Cleaning of instrument after every use.
• HPLC Inline filter cleaning – monthly.
• HPLC suction filter cleaning – monthly.
7. Formats
7.1 Format for Cleaning of HPLC inline filter
Sr. No.
HPLC No.
Number of filters
Cleaning start time
Cleaning end time
Done by
Checked by
7.2 Format for Cleaning of HPLC suction filter
Sr. No.
HPLC No.
Number of filters
Cleaning start time
Cleaning end time
Done by
Checked by
Reference:
Reference: 21 CFR PART 211 Subpart D – Equipment
To read more similar SOPs, click here