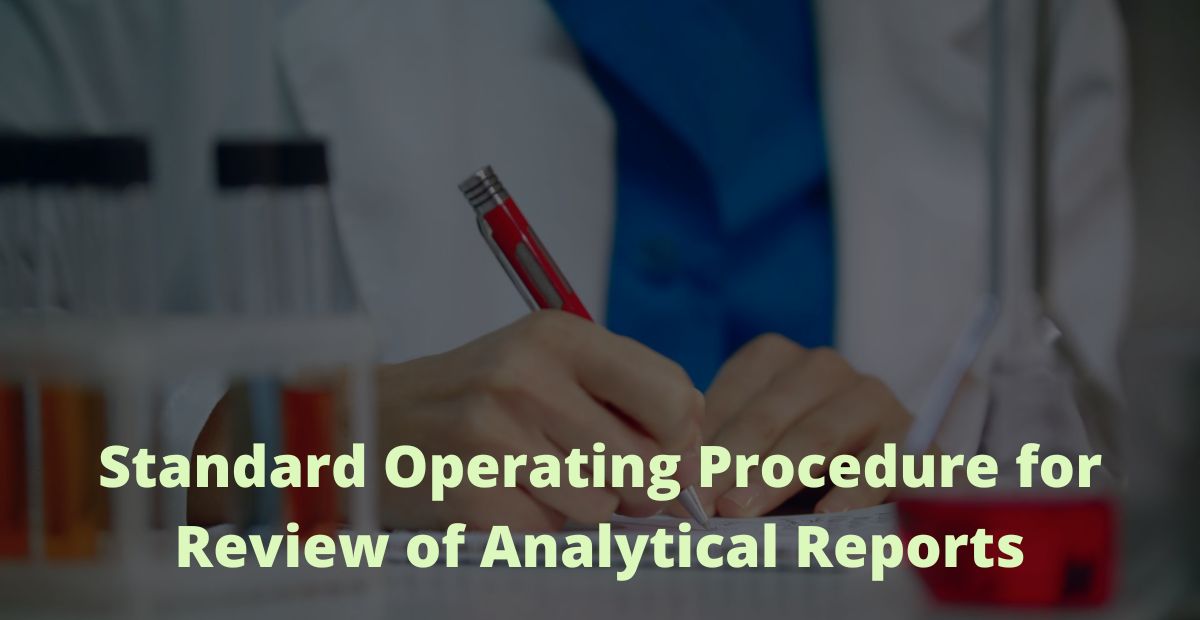
Standard Operating Procedure for Review of Analytical Reports
1.0 Purpose:
To lay down a procedure for Review of Analytical Reports.
2.0 Scope:
The scope of this SOP is applicable for Review of all the Analytical Reports in Quality Control Department and microbiology department at [company name].
3.0 Responsibility:
QC – Personnel: To perform the testing and data input. To Performs a primary review of data.
Lab QA Reviewer: To perform a complete analytical package review by comparing electronic and analytical raw data for accuracy and completeness
Supervisor – QC: To perform a complete analytical package review by comparing Electronic and analytical raw data for accuracy and completeness.
Section in-charge / Designee: To perform documentation check to assure completion of all requisite reviews and signature fields. To ensure that the correction are verified. To ensure that initial data is reviewed and signed off with all complete information and accuracy. To approve the analytical report.
Head – QC/ Designee: To approve the analytical report. To ensure the compliance of SOP.
QA Personnel: To ensure that initial data is reviewed and signed off with all complete information and accuracy before approval of copy 2.
4.0 Definitions:
• Performed By (e.g. Analyst): Action performed and executed.
• Verified By: A second person was present during the execution of the activity and physically verified that the activity was completed as recorded.
• Reviewed By: Review of data and the activity performed by an independent person for data accuracy, completeness and compliance to procedure.
• Checked By: To ensure Documentation review (performed after the action is completed) by a third person as soon as the documentation is completed.
• Approved By: To ensure and serves as a secondary documentation review for document completeness.
5.0 Procedure:
5.1 During the analysis, the analyst shall enter the observation in the analytical worksheet online.
5.2 The balance printouts for weights and chromatograms shall be attached separately along with entire Raw Data.
5.3 After completion of the analysis, the analyst shall review the report for completion as per checkpoint listed in the checklist and handover the report to the respective Reviewer.
5.4 Analytical Reports of Raw Material, Stability, Working Standard Qualification, Packaging Material, Semi-Finished, Finished Product, Process Validation, Analytical Method Validation, Analytical Method Transfer and Analytical Method Verification shall be reviewed as per checkpoint listed in the checklist (but not limited to) by respective reviewer and checklist shall be attached to analytical report.
5.5 Analytical reports of Microbiology department shall be reviewed as per checkpoints listed in the checklist (but not limited to) by respective reviewer and checklist shall be attached to analytical report.
5.6 Report reviewer shall have adequate training on GMP requirements.
5.7 QC Personnel shall check online activity as per respective format “Reviewer check list for checkpoint during online review in quality control department” and same activity shall be checked by Lab QA reviewer.
5.8 Hard copy of HPLC, UPLC, IC, GC, UV, IR and Differential Scanning Calorimeter Instrument Chromatogram/Printouts shall be reviewed by reviewer against Electronic Data whenever required.
5.9 Electronic raw data shall be checked thoroughly.
5.10 During review of Analytical report, Reviewer shall check following details (Not Limited to):
• Date of Analysis
• Start time of Sample set
• Sample details
• Instrument Method
• Processing Method
• Audit Trails
• System suitability criteria
• Analytical worksheet revision number against current specification etc.
5.11 During review, reviewer shall ensure there are no unprocessed injections in particular empower project of sample set by creating filters in chromatographic software.
5.12 During review of Analytical report, Reviewer has to check/ensure that no unprocessed injections found for particular sample set run on chromatographic software. This is to be ensured through filters facility/function available in chromatographic software.
5.13 In addition to unprocessed injections check, reviewer has to ensure unavailability of aborted & single injection run in particular sample set.
5.14 Reviewer shall check all documents such as log books and working standard entries.
5.15 Reviewer shall confirm compliance of report as per SOP for Good Documentation.
5.16 Reviewer shall review all calculations, chromatograms and other raw data for its adequacy with respect to GMP requirements.
5.17 If any error is identified in report, it shall be notified to analyst and report shall be returned to analyst for necessary rectification.
5.18 The analyst shall make necessary rectification and return report to Reviewer for checking.
5.19 For analysis which is not done through LIMS, reporting shall be done in manual worksheet provided for respective products and forwarded to Reviewer for review. The same shall be approved by Head – QC/Designee.
5.20 After reviewing Analytical Report, it shall be signed by respective Reviewer wherever Checked By is required.
5.21 The analyst and reviewer shall check any OOS/OOT/significant change as per criteria defined in respective SOP.
5.22 Reviewer shall review Audit check report, Result Audit trail and Sequence Audit trail attached with Analytical report. During review of Audit check report reviewer shall check processing ID, Instrument ID, Sample set ID, No. of stored results, altered results, Sample set altered, instrument method parameter and Processing method parameter details.
5.23 The reviewer shall verify the instrument method and processing method in the audit check report, which is printed for every sequence and reviewed post-analysis to verify the instrument method parameters used for analysis.
5.24 After completion of all the tests and result recording, the Raw Data Sheet/Electronic Worksheet shall be checked by the reviewer and approved in LIMS.
5.25 The reviewer shall hand over the analytical report to another reviewer for further review; this reviewer shall perform a complete analytical package review by comparing electronic and analytical raw data for accuracy and completeness.
5.26 The reviewer shall sign and date, and return the analytical report to the supervisor for final approval.
5.27 In case of Raw Materials and Packaging Materials, the approval is done by Head – QC/Designee, and for Semi-Finished and Finished Products, the final approval is done by Head – QA/Designee.
5.28 During lab events such as an incident, OOS, significant change, or for any repeat testing, the analyst has to print worksheet copy no. 2 from LIMS for reporting of repeated test. In such cases, section in charge/designee and QA person approving worksheet copy 2 must ensure that initial data is reviewed and signed off with all complete information and accuracy. After ensuring the completeness of initial data, worksheet copy 2 shall be permitted for repeated analysis.
6.0 Acceptance Criteria:
Not applicable.
7.0 Frequency:
While checking of all the Analytical Reports.
8.0 Format for recording:
8.1 Reviewer checklist for check points during review of analytical reports of quality control department.
a. All tests performed as per the current revision number of Specification.
b. For all tests, Analytical Balance Printouts are attached.
c. All chromatogram attachments as per respective SOP.
d. B. No. and AR No. verified on chromatograms with respect to details mentioned in worksheet.
e. Audit check report checked.
f. Cancellation of any chromatogram is justified and authorized.
g. Reintegration/manual integration authorized.
h. Any stock solution used in analysis is within valid period (Like SST, Volumetric solution, etc.)
i. Whether analysis is completed within expected date of analysis including tolerance period in stability study.
j. Instrument Logbook entry verified against raw data.
k. OOS/ OOT/ significant change verified as per criteria defined in respective SOP.
l. Working standard/ Impurity standard/ Reference standard/ column usage entry verified in LIMS.
m. Electronic Raw Data checked thoroughly in LIMS.
n. For any repeat analysis, reference QMS No__________________.
o. Sign & date on all chromatograms and raw Data verified.
p. Accuracy and completeness of Data are verified.
10.2 Reviewer checklist for check points during review of analytical reports of Microbiology department”.
a. Was the product name and SOP/Specification ID, Rev. No. found to be correct?
b. Was the media reconciliation entry verified against raw data?
c. Was the membrane filter used for analysis within its expiry date?
d. Were the media and accessories used during analysis, sterilization load no. verified from the sterilization record?
e. Was the correct sample quantity used for analysis as per SOP/ Specification/ Protocol for analysis?
f. Were test supporting printouts/traceability attached with the worksheet?
g. Were Batch No./Control No. and AR No. verified on raw data with respect to the sample inward register?
h. Were Entry/Exit entries verified against raw data?
i. Was CSE/LRW/Lysate used for BET test within its expiry period?
j. Was the sterilization cycle number for assembly verified against raw data?
k. Was any sample cancellation justified and authorized?
l. Were signs and dates on all supporting printouts and raw data verified?
m. Were TOC results print (hard copy) verified against electronic data?
n. Were LBPC results print (hard copy) verified against electronic data?
o. Were Vitek Identification results print (hard copy) verified against electronic data?
p. Was the instrument usage log book entry verified against raw data?
q. Was audit trial history reviewed?
r. Was alarm history reviewed?
s. Was incomplete or missing data (if any) reviewed?
t. Was any incident/OOS/Deviation (if any) related to the test reviewed?
u. Were all tests performed as per Specification/SOP/Protocol?
v. Was the accuracy and completeness of Data reviewed?
w. Was Electronic Raw Data checked thoroughly in LIMS?
10.3 Instrument Specific reviewer checklist for check point during online review in quality control department.
A. Autotitrator:
• Ensure that the correct method is selected for analysis.
• Check that the correct electrode is selected for analysis.
• Before starting the analysis, check and ensure that the tubing and burettes are free from air bubbles.
• Physically verify the electrode and stirrer for breakage.
• Ensure that the electrode has filling solution up to the optimum level.
• Check that the electrode cap is open during titration.
• Check the non-aqueous electrode for loosening of the diaphragm (if tight, it should be loosened).
• Check for the presence of an NRV (Non-returnable Valve) and any physical damage.
• Check for the use of an appropriate pipette for adding solutions.
• Use an amber-colored bottle for storing light-sensitive volumetric solutions.
• Ensure that the electrode, titration vessel, and magnetic stirrer are cleaned.
• Ensure that a closed titration vessel is used for analyzing moisture-sensitive materials.
• Ensure that the volumetric solution is degassed.
• Review electronic data against hard copy data, audit trail, alteration, modification, etc.
2. IR:
• Check background before starting analysis.
• Review electronic data against hard copy data, audit trail, alteration, modification, etc.
3. UV:
• Ensure that the correct method is selected for analysis.
• Review electronic data against hard copy data, audit trail, alteration, modification, etc.
4. Atomic absorption spectrophotometer/Surface area analyzer/TGA: Applicable/Not applicable
• Check if sufficient pressure is found on control panel display.
• Review electronic data against hard copy data, audit trail, alteration, modification, etc.
5. ICP-MS:
• Verify cleaning of Storch, Skimmer cone, Nebulizer, Spray Chamber, Bonnet.
• Check water level in chiller and its connections (tubing) to instrument.
• Check if sufficient pressure is found on control panel display for argon.
• Ensure sequence and instrument method are as per specification/protocol.
• Review electronic data against hard copy data, audit trail, alteration, modification, etc.
6. Electrophoresis:
• Verify preparation of electrolyte/mobile phase and electrolyte bottle labeling.
• Check column taken for analysis as per specification i.e. column name, length, particle size.
• Check injection pressure.
• Prepare all solutions as per specification.
• Ensure sequence vial number matches actual vial position in electrophoresis vial tray.
• Ensure correct batch number sample is taken for analysis (sample batch number reflects in sequence).
• Review electronic data against hard copy data, audit trail, alteration, modification, etc.
7. HPLC/ GC/ UPLC/ GCMS/ IC:
• Review processed data, unprocessed data and sign-off activity,
• Review channel lock status
• Check chromatograms for proper peak shape, baseline and identified peak name and integration parameters
• Review audit trail, alteration, modification etc.
8. DSC/Alpine Air jet/Polarimeter/Spectrofluorometer/Refractometer/Microwave digester/Melting point/Universal testing Machine
• Review electronic data against hard copy data, audit trail, alteration, modification etc.
9. Malvern analyzer:
• Verify intensity of lens
• Check air flow
• Perform manual measurement (cleaning) activity
• Review electronic data against hard copy data, audit trail, alteration modification etc.