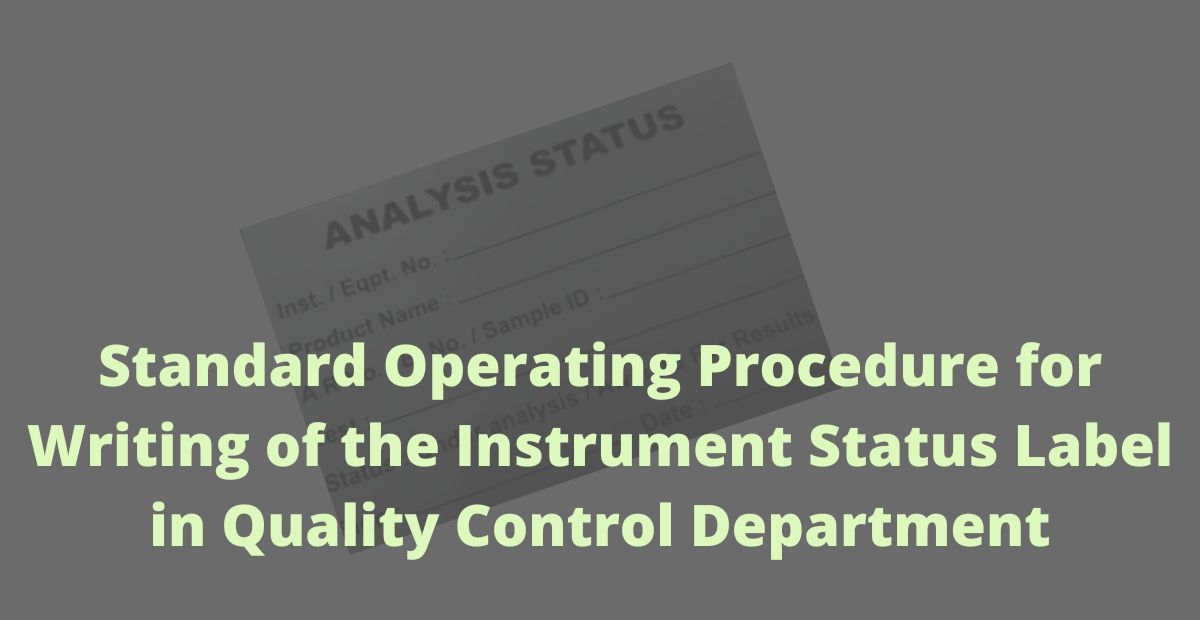
Standard Operating Procedure for Writing of the Instrument Status Label in Quality Control Department
1.0 Purpose:
To lay down a procedure for Writing of the Instrument Status Label in Quality Control Department.
2.0 Scope:
The scope of this procedure is applicable for writing of the Instrument Status Label in Quality Control Department.
3.0 Responsibility:
QC Personnel: To update the instrument status label
Manager QC/ Designee: To check the information written on the instrument status label.
4.0 Definitions:
NA
5.0 Procedure:
- The information written on the “Instrument Status Label” should be clear and readable.
- The information written on the “Instrument Status Label” should be based on the current activity being performed on the instrument.
- A Marker Pen (Blue / Black) should be used for writing on the “Instrument Status Label”.
- Prior to the start of an activity, the QC person using the instrument should write the details on the “Instrument Status Label” placed on it.
- The “Instrument Status Label” should have the following details:
- Instrument Code
- Product
- Batch Number
- Analytical Report Number (A.R. No.)
- Test
- Signature
- Date
- After completing a task, if the instrument is to be used by another QC Person, it is their responsibility to clear the previous status and rewrite the current instrument status.
- In case the instrument is idle, the QC person should write “No Activity” along with their Signature and Date on the “Instrument Status Label”.
6.0 Acceptance Criteria:
6.1 Not applicable.
7.0 Frequency:
7.1 As and when required.
8.0 Format for recording:
8.1 Format for “Instrument Status Label”
Instrument Name :
Inst. Code : ____________
Product :
Batch No. :
A.R. No. :
Test :
Sign :
Date :