Standard Operating Procedure for Material Location in Warehouse
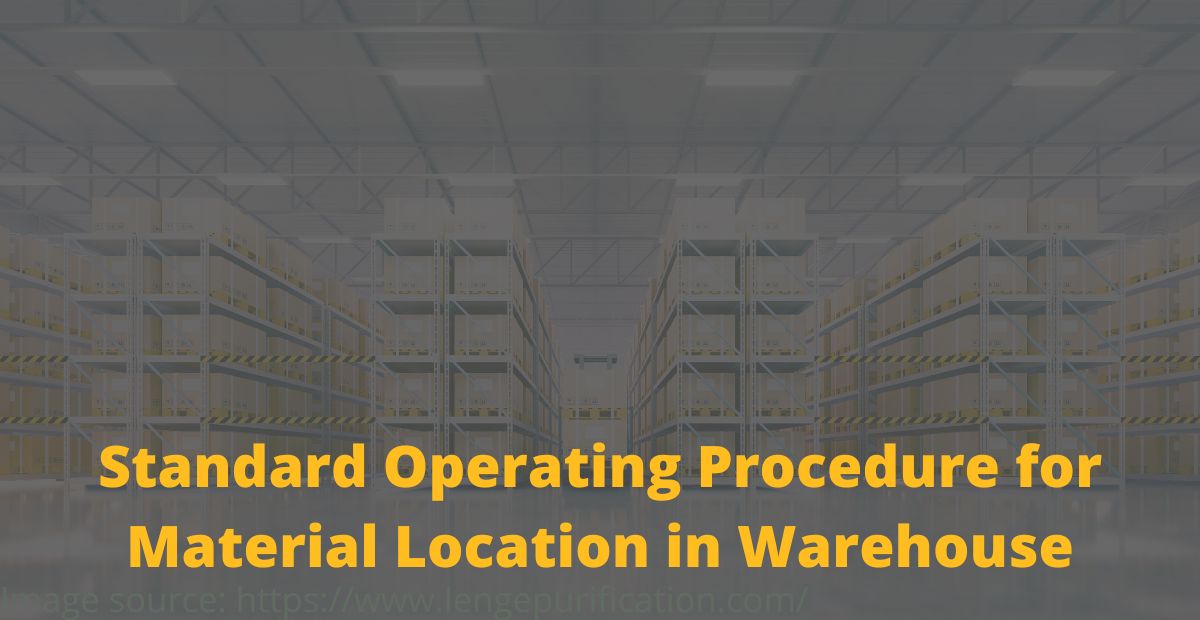
Standard Operating Procedure for Material Location in Warehouse
1. Purpose:
To lay down a procedure for defining location for Raw material, Packing material and Finished Goods in the pharmaceutical warehouse.
2. Scope
The scope of this SOP is applicable for defining location for Raw material, Packing material and Finished Goods in the pharmaceutical warehouse at [company name].
3. Responsibility
Warehouse Person: Locating the material as per the procedure
Warehouse supervisor: To monitor material location control.
Head Warehouse: Effective implementation of SOP
4. Definitions
Not applicable
5. Procedure
• Always store material on clean pallets before transferring it on the racks.
• While placing the material on the rack, make entry of location number in the location chart/ location chart logbook.
• In the location chart/ location chart logbook enter the material name, material code, batch number/ A.R. No., date on which material is placed.
• Place the material as per the material status such as “Quarantine”, “Under test” or “Approved”.
• Material should be stored in the area as per applicable storage condition, such as ambient (Specify temperature that company has decided as ambient), controlled storage area, cool place, cold room, -20 Deg. C, -80 Deg. C, or any specified condition.
• While movement of material for dispensing, transferring of material from one location to another location, update the material location chart/ material location logbook.
• Numbering of rack shall be done for rack line, rack column and level of height. Rack numbering system shall be start from A1001, A1002, A2001, A2002, etc. In this numbering system, ‘A’ is rack number, 1 is column and 001 is height level..
• Material shall be placed on location and entry shall be made in respective logbook when new material receives, quarantine material transfer to approved stock or approved material goes under retest, etc.
• Quarantine label shall be affixed by warehouse person, under test, approved or reject status material are affixed by quality control staff.
• Material shall be stored at the area that is covered during the storage area mapping study. On each rack and pellet, material shall not be stored beyond the applicable height [Specify the height as per respective company safety norms].
• If space is not sufficient in the racks, it can be placed on the floor that is covered under the mapping study and those are numbered.
• Ensure that accurate details are written in the material location chart/ material location logbook. It shall be updated contemporaneously.
• In case of new rack is required to add, it shall be added through change control system. New location shall be covered under mapping study by repeating mapping study.
• Location chart/ material location logbook shall be issued from QA and once the document usage over, it shall be returned to QA for future reference.
• In logbook for material location chart shall be updated by warehouse person and verified by warehouse supervisor.
• In case of any specific status rack is full (Example – Approved area is full), material can be stored in other status area with adequate indication on the rack. For example, rack shall be temporary labeled with green color board with specifying location range.
• This temporary arrangement shall be documented in the material location chart logbook with remark that such and such racks status were temporarily change from “Quarantine” to “Approved” for specified duration.
• No rejected material shall be stored at Quarantine area or Approved area.
6. Frequency
Location chart shall be updated as and when new material received or material transferred from one rack to another rack or material is permanently removed from the racks.
7. Formats
7.1 Material location chart/ material location logbook
Location No.:
Material Code/ Batch No.
Material Name
Date of material in
Remark (if any)
Entry Done by
Entry verified by
Date of material out
Entry Done by
Entry verified by