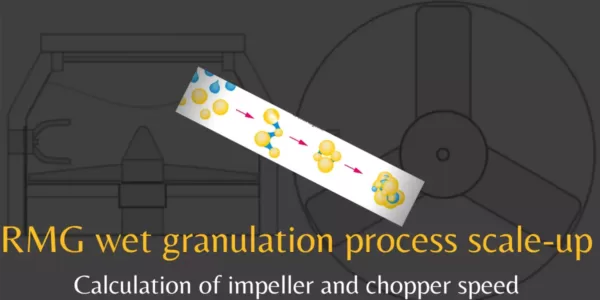
Calculation of impeller and chopper speed during RMG wet granulation process scale-up
High-shear Granulation or Rapid Mixture Granulation process for Immediate Release (IR) formulation
Know how for the impeller and chopper speed scale-up rule for wet granulation process is most important for pharmaceutical technology transfer team and formulation research and development team.
Any change in the pharmaceutical environment is done through change management system. While assessing the change during scale-up, evaluation through following scale-up rule
Rapid Mixture Granulator (RMG) Impeller speed:
Various publications discussed about approach for impeller speed scale-up rules. These are Rahmanian, Ng, et al., 2008; Horsthuis, van Laarhoven, van Rooij, & Vromans, 1993; Rekhi et al., 1996; Faure et al., 2001; Hassanpour, Antony, & Ghadiri, 2007; Tao et al., 2015; Tardos, Hapgood, Ipadeola, & Michaels, 2004).
The most commonly used formula for scaling impeller speed is power law correlation as shown in following equation.
Where,
RPM1 and RPM2 are the impeller speeds in revolutions per minute of first and second granulator
D1 and D2 are the impeller diameters of first granulator and second granulator (in inch)
n is a constant depending on the rule: (i) for constant tip speed, the value of n = 1.0; (ii) for constant shear stress, the value of n = 0.8; (iii) for constant Froude number, the value of n = 0.5.
Constant tip speed | 1.0 | Produces agglomerates of comparable strength. |
Constant shear stress | 0.8 | The difference in agglomerate strength distribution produced in different scales becomes progressively larger for the constant shear stress and constant Froude number rules, respectively. |
Constant Froude number | 0.5 |
Hence, it can be concluded that the constant Froude number rule is unsuitable for the scale-up of high-shear granulators because the interest is keeping the crushing strength constant.
Furthermore, when the conditions of constant shear stress are used to scale up the granulator, the granules produced in smaller size granulator are weaker than those of larger capacity granulator.
Reference: Article on Scale-up of High-Shear Mixer Granulators, N. Rahmanian, B.H. Ng et al., 2008
As per article by Rekhi et al., 1996, batches manufactured at different scales showed similar granulation and tablet properties where high-shear mixers used with geometric similarity. The important factors that should be considered in scaling up a when using high-shear granulation process are as follows:
- Constant impeller speed by adjusting the tip speed constant (i.e. constant radial velocity)
- Linearly scaled-up volume of granulating fluid based on batch size (constant % water amount)
- Adjustment of the granulation time (massing time) based on a ratio of the impeller speeds from one scale to the next.
Good in-process controls and the use of engineering controls are very much vital for successful scale-up. Size and shape of mixing chambers and impeller and chopper configurations differ in various types of high-shear mixers hence, the results while scale-up cannot necessarily be extrapolated to another high-shear mixer, even though having same operating principle.
The study demonstrates good scalability of granules properties such as bulk and tap density, blend uniformity, particle size distribution, and tablet dissolution.
In case of modified release formulations, apart from critical process parameters, the excipients responsible for modified release properties also play a significant role. Hence, constant impeller tip speed ratio will not work in the scale up of such Formulations.
RMG Chopper speed:
Similar to the impeller speed scale-up, the scaling-up of chopper speed can be done using same tip speed. When doing this the granules will be chopped with similar impact forces. Chopper is usually started after the fluid addition is complete. This will provide kneading energy to the granulation. The chopper use to reduce lumps of the granulated wet mass. The chopper blades rotating at high speeds fragment the dense mass into smaller granules.
Wet Granulation time:
Granule growth and consolidation are assumed to take place at the high-impact and high-shear zones between the tips of the blades and the vicinity of the wall region of the granulator. Thus, the granulation rate increases (or processing time decreases) with increasing wall surface area. In contrast, the larger the quantity of material available for granulation, the longer the granulation processing time will be needed. Therefore, it is assumed that the granulation rate is inversely proportional to the volume of the sample.
Reference: Article on Scale-up of High-Shear Mixer Granulators, N. Rahmanian, B.H. Ng et al., 2008
As per the same literature, recommended method to scale granulation time in the granulator can be calculated using the following equation below:
Where,
1 is the original granulator and 2 is the scaled-up granulator,
t1 and t2 are respective granulation time
S1 and S2 are the internal wall surface area of respective granulators
V1 and V2 are their bulk mass volumes respectively