
Seven step process of Investigation and CAPA Management
Before starting the process of investigation, let’s understand briefly about Corrective Action and Preventive Action (CAPA), its linkages with the guidance and regulations, and how it links with the investigation. We shall also look at a few examples of the regulatory citation because of deficiencies related to investigation and CAPA. In this article, most of the examples and regulatory linkages are used with respect to the pharmaceutical industry. However, a similar approach can be used to carry out an investigation and defining the CAPA.
Introduction to the Corrective Action and Preventive Action (CAPA):
To introduce Corrective Actions and Preventive Actions (CAPA), let’s understand few definitions.
“Correction” means an action to mitigate an identified non-conformance
- The Correction and corrective action can be combined
- Examples of corrections are – re-grading, inspection, reworking, etc.
“Corrective action” means an action taken to remove the cause of an identified non-conformance or other objectionable condition
- The cause of non-conformance could be one or more than one
- Corrective action is an action required to prevent the same or similar recurrence
- Correction and corrective action are different terminologies
“Preventive action” means an action that eliminates all potential causes of non-conformance or other objectionable condition
- Potential causes for non-conformance may be one or more
- Action is taken to prevent occurrence is called as preventive action
“Mature Quality system detects problem before it occurs and required controls put in place”
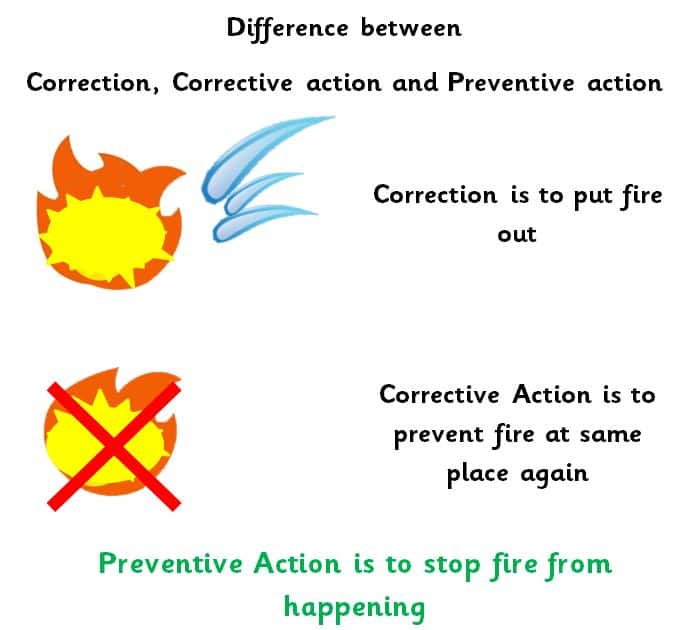
Evolution of CAPA:
The CAPA system evolved gradually from reporting the events to the risk-based life cycle approach in the regulatory environment. The diagram alongside is self-explanatory.
Reference: www.fda.gov
Regulations and their linkages with CAPA:
When you look at the regulations, US, Europe, or any other regulations, all the regulations are linked with the requirement of Corrective Action and Preventive Actions (CAPA).
US Regulation: 21 CFR Part 211.22 – Responsibility of Quality Unit | ![]() |
US Regulation: 21 CFR Part 211.100 – Written Procedures | ![]() |
US Regulation: 21 CFR Part 211.192 – Production record review | ![]() |
European Commission Directive: 2003/94/EC | ![]() |
European Commission Directive: 2003/94/EC | ![]() |
EudraLex: Vol 4: Chapter 1 Pharmaceutical Quality System | ![]() |
EudraLex: Vol 4: Chapter 1 Pharmaceutical Quality System | ![]() |
Example of Investigation and CAPA deficiencies:
Many organizations came across the situation of getting the FDA Warning Letter for Failure to include adequate documentation during an investigation. I have removed the name of an organization in this article.
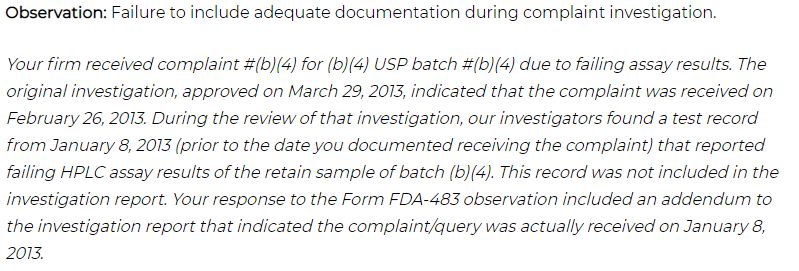
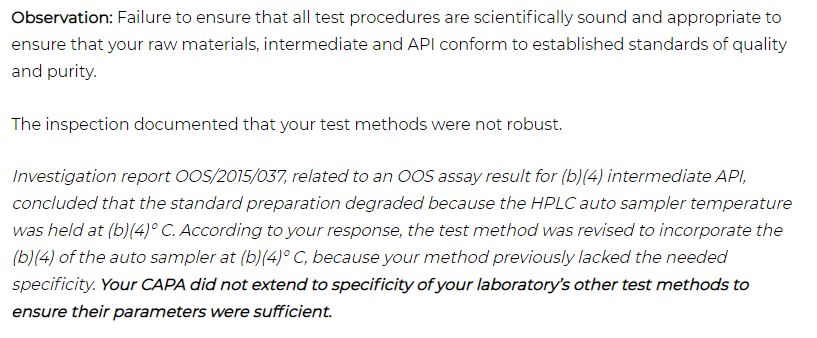

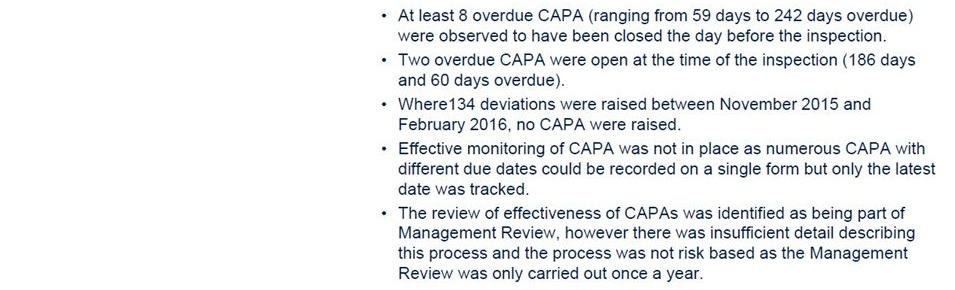
Process of investigation and identification of CAPA:
Here we have tried to simplify the process steps to investigate using seven steps method. These steps are identifying an event, risk evaluation, investigation of an event, root cause analysis, defining an action plan, implementation of planned actions, and finally, closure of an event. The event could be process deviation, laboratory event, complaint investigation, or any other kind of investigation.
The seven steps method of investigation are as follows:
Step 1: Identification of an event
Step 2: Risk evaluation
Step 3: Investigation of an event
Step 4: Root cause analysis
Step 5: Defining an action plan
Step 6: Implementation of planned actions
Step 7: Closure and effectiveness review
Let’s understand each step one by one in detail in the following sanction of an article.
Step 1: Identification of an event
Identification of the problem includes clearly defining and explaining the problem. This step is crucial because the correct definition of the problem will take you in the right direction during the investigation. The incorrectly defined problem will take you in the wrong direction, and the root cause of an event would be challenging to identify.
Problem: The term problem means “Non-conformity, defect or un-fulfillment of a requirement in a product or system or process”.
Identification description must include source, complete information of event or problem, and collection of documentary evidence.
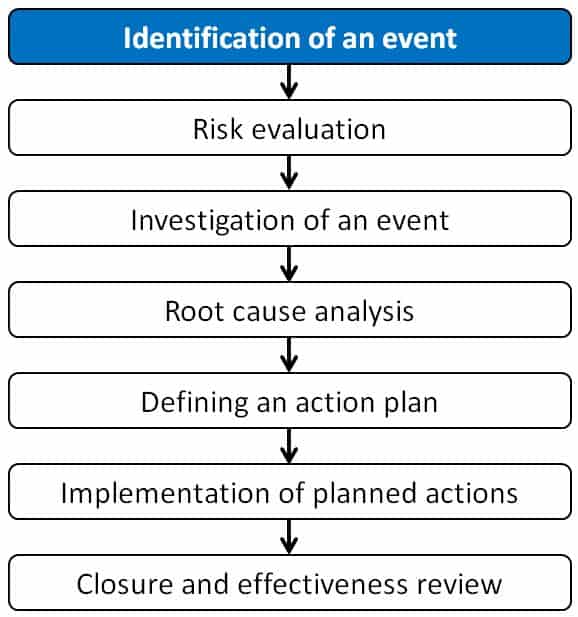
To identify the complete information, we can use a simple tool called 5W2H. This methodology will help to describe the event very precisely.
Let’s understand each element of as 5W2H.
What: Details of abnormality
When: Date, Shift, and Time of Event
Where: Location/ Plant/ Line
Which: Machine/ Product/ Batch number
Who: The person who identified or noticed the event
How: Mode or situation of occurrence
How Many: Batches, number of times
An internal source or external source could make the problem identification. The source of CAPA could be deviations, internal audits, external audits, Annual Product Quality Review (APQR), etc. Various sources of issues are explained in the following schematic.
Step 2: Risk evaluation
The identified problem needs to be assessed for the risk. The risk assessment is required to be done to determine the need for immediate action/ countermeasure, level of actions, and investigation required. A potential risk could be the product safety, efficacy, quality, material rejection, yield, delay in processing, etc.
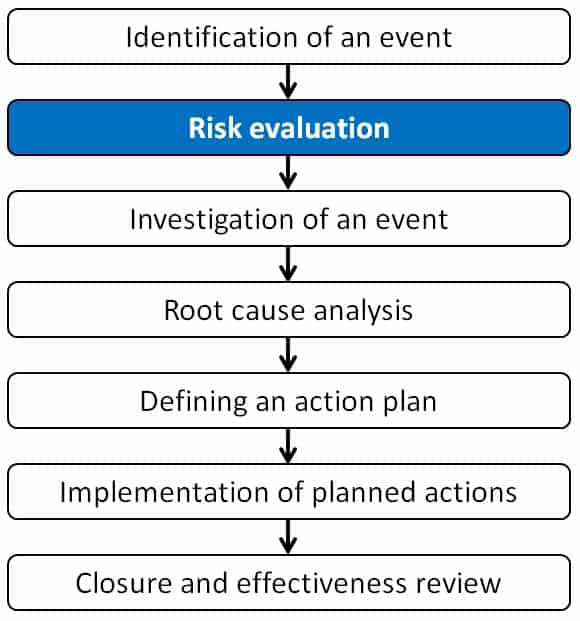
- Potential impact of the event
- Risk to company and customer
- Remediation action
You can classify a risk using a qualitative or quantitative approach. In broad terms, risk categories are Critical, Major, or Minor. The most preferred method of categorization of risk is the quantitative approach. One can apply the tools such as the Failure Mode Effect Analysis (FMEA) where, the Risk Priority Number (RPM) calculated using the Severity (S), Detectability (D), and Probability of occurrence (P).
Remedial actions/ countermeasures – The required measures are decided based on potential impact and risk assessment. The risk assessment helps to understand whether immediate action is needed to remedy the situation until a permanent solution or not.
Immediate communications – Timely inform to all the concerned authorities is an essential step. In case of a critical event, the defect may result in the product recall or restriction in the product supply. Such an event needs immediate communication to the customers, regulatory agency, and relevant stakeholders who could have been affected by the event.
In some cases, remediation action may be sufficient. It does not require additional CAPA. The event can be closed with logical and scientifically sound rationale.
Step 3: Investigation of an event
Definition of investigation
Steps of preliminary investigation and detailed investigation
- Write down an objective
- Formation of a cross-functional team
- Collection of supporting information and evidence
- Documentation
- Decision on CAPA
Objective: The objective of a preliminary investigation is to collect the maximum possible and available information. The information is about the event and clues responsible for the cause of an event. An objective statement is critical to draw the investigation path.
Cross-functional team: It is essential to build a cross-functional team as quickly as possible to collect first-hand information. The team members should know the subject, analytical thinking, logical thinking, training, experience, or a combination of these skills.
The collection of first-hand information and relevant data is critical to identify the root cause. Take care that all possible data is collected and nothing is overlooked. Data collection may include area, equipment, associated lot numbers, environmental conditions, personnel involved in the process, prior knowledge and training of involved personnel, batch document, lab notebook, or any physical condition of the area or object associate with the event.
The investigation should cover a comprehensive review of all the circumstances such as Machine, Material, Method, Measurement, Mother Nature, and Man.
The data should be organized in such a manner that comparison and data analysis can be done quickly and easily.

Once the data is collected, data analysis should be done using statistical tools such as standard deviations, histograms, graphs, or other relevant non-statistical techniques. These tools will help to understand about potential causes or root cause of the event.
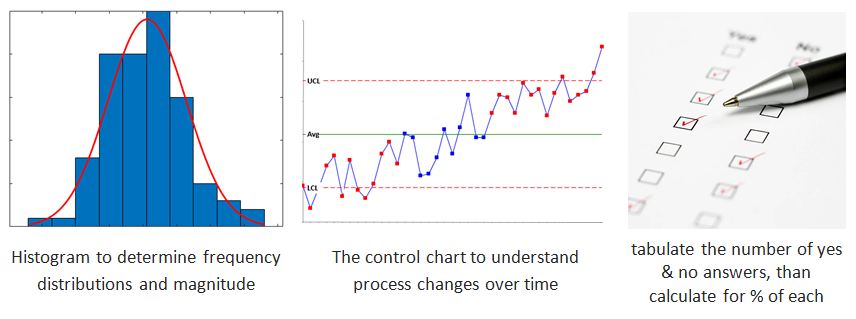
Decision on the further root causes analysis or investigation:
Based on the preliminary investigation, data compilation, and data analysis, the event can be closed. Carefully evaluate such a situation before deciding to close an event to avoid any regulatory non-conformance during the inspection. The following could be scenarios where the event can be closed at this stage
- The incident happened for the first time, and the risk associated with the incident is negligible.
- A similar incident had occurred in the recent past, to which corrective action and preventive actions are under implementation.
Step 4: Root cause analysis
If the root cause is not identified after the preliminary investigation, the root cause analysis can be done as explained in this section.

- Collecting relevant data
- Investigating all possible causes
- Determine root cause/ most probable cause
Regulatory reference on root cause analysis
Common Statistical Techniques used during the investigation are:
(i) Run charts, (ii) Control charts, (iii) Pareto charts, (iv) Mean, (v) T tests for comparisons, (vi) standard deviation, (vii) Experimental design (DOE), (viii) Visual tools such as fishbone diagrams, spreadsheets, scatter plots, histograms, etc.)
Reference: www.fda.gov
Pareto charts:
Vilfredo Pareto invented a Pareto chart; that is why the chart is called as Pareto chart. The chart contains bars and a line. Bars are arranged in descending order. These bars are the individual values. The line is plotted using the cumulative total.
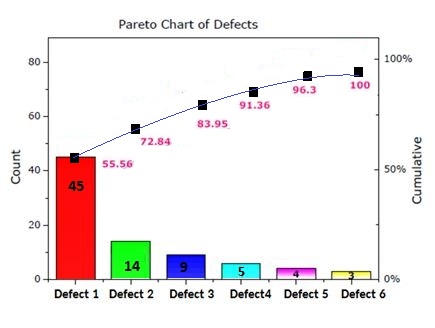
This chart helps to indicate the frequency of events and their overall impact.
Histogram:
The histogram was first demonstrated by Karl Pearson. The tool represents the distribution of data. It provides an idea about the distribution probability of a variable, continuous data.
Step 1: Bin the range of values. The bins are consecutive and non-overlapping intervals of variable data.
Step 2: Divide values into intervals.
Step 3: Count how many values fall into each bin.
Types of Histogram
Different types of histograms are demonstrated as follows.

Commonly used root cause analysis tools are as follows:
- Fishbone diagrams/ Ishikawa Diagram
- Why-why or 5 “whys”
- Fault-tree analysis
- Among others
Reference: www.fda.gov
Fishbone or cause-and-effect diagram
(a) Other names of Fishbone diagrams:
(i) Ishikawa diagram
(ii) Fishikawa diagram
(iii) Cause-and-effect diagram
(iv) Herringbone diagram
Crated by: Professor Kaoru Ishikawa
Year: 1960s
Purpose: To solve problems at the Kawasaki shipyards
Widespread use in current century:
Identify underlying causes of near-miss, events, incidences, complaints, deviation , problem-solving, adverse event, etc.
Click to this link to know more about Fishbone or the cause-and-effect diagram
Why-Why or 5 Why analysis:
Why-why or 5 “why” technique is the most powerful tool for problem-solving and root cause analysis.
The tool is invented by: Sakichi Toyoda, the Japanese industrialist. The founder of Toyota Industries
Year: 1930s
Popularized in the year: 1970s

Let’s understand how the method works.
In this article, a three-step process is described to carry out 5 Why or Why-Why analysis.
Step i: When a problem is identified, create a clear and crisp problem statement by asking questions such as What is going wrong, when it happen, where did it happen? Who found the problem?
- Include process where defect produced
- Also, include Why problem not detected
Step ii: Move backward by asking why every time. To identify the root cause try to identify within the process or a system failure. Opportunity for system or process improvement is generally real root causes. Exclude operator/ staff error and try to find process failures that ensured the operator made an error.
Step iii: Bad process or system will beat good people hence; focus on the process and system issues rather than people.
KEY to the five why or why-why technique is to Focus on the cure, not the symptoms
Do it the with team, don’t do it alone…
This is a simple and effective tool, but a word of warning. Do not try it at your desk and do not do it on your own. However, don’t overcrowd with 15 to 20 people.
1st Why | Clear problem statement. 1st ‘why’ should be short. Do not justify it at this stage. Write even though it is obvious to you. It may not be obvious for others. |
2nd Why | To get into the technical part. The explanation can branch out to several different potential causes. For each of the probable causes, identify the remaining 3 Whys. |
3nd Why |
|
4th Why |
|
5th Why |
|

Example of Five why or why-why:
Content from: https://www.educational-business-articles.com/
You can refer to the practical example video where an issue at Jefferson Memorial was solved using a why-why analysis.
Click on this link to see the video by ASQ TV.
Step 5: Defining an action plan
As per 21 CFR 820.100(a)(3), the actions need to derive to prevent a recurrence. The actions can be correct action or prevent or both. These actions shall eliminate the potential for product non-conformity and other quality problems once it is implemented.
Action may either of following or in combination
- No further action necessary
- Correction
- Corrective Action
- Preventative Action
FDA Guidance:
To generate solutions, one can use a free-brainstorming method or can use a structured approach called SCAMPER.
Brainstorming:
Brainstorming is a team-driven process used to generate fresh and creative ideas for problem solution
- Do not criticize so that most of the members can give ideas freely
- It produces many solutions for one problem
The following rules are necessary for every brainstorming session.
- Every suggestions count
- Do not drill down on proposed ideas
- Do not demoralize anyone using killer words
- Encourage all participants to give ideas – nothing right or wrong at this stage
- Allow all participants to complete their ideas – listen to everyone
SCAMPER:
Proposer of SCAMPER: Alex Osborne in 1953
Further Developed by: Bob Eberle
Year: 1971
Published in the book: SCAMPER -Games for Imagination Development
SCAMPER
Substitute | Substituting part of the product or process for something else |
Combine | Combining two or more parts of the product or process to make something new |
Adapt | Parts of the product or process could be adapted or way to change the nature of the product or process |
Modify or magnify | Modifying part or the entire product or process |
Put to other uses | You might put a certain product or process to other use |
Eliminate | You eliminate certain parts of the process |
Rearrange or Reverse | Parts of the product or process worked in a reverse way, or it sequenced differently |
Step 6: Implementation of planned actions
Implementation
As per 21 CFR 820.100(a)(5), Whenever issues are identified in the procedures or methods, required changes need to be implemented, and recording should be done.
Communicating CAPA Information
As per 21 CFR 820.100(a)(6), information related to quality issues or non-conformance should be communicated to those who are accountable for the adequacy of the product quality and who could prevent reoccurrence.
Employee training is a critical part of any change implementation and should be a part of the action plan. For effective implementation of the CAPA, all modifications and changes made in the system must be communicated to all persons, departments, suppliers, etc. that were or will be affected.
Execution of implementation plan and useful tools:
- Activity listing: List down all identified actions
- Prioritize: Prioritization can be done with the help of tools such as effort benefit analysis or cost-benefit analysis.
- Planning and mapping activities: The best way to plan the activities is to use a structured approach to organize activities and broken down into smaller tasks. Various program management methods are available such as Gantt chart, Process Mapping, Value stream mapping, etc.
- Gantt chart: A Gantt chart is a tool used for the planning and scheduling of activities. It is useful for simplifying complex tasks.
- Process mapping: A process mapping is a way of planning and management by visually describing the flow of work.
- Value stream mapping: A value stream mapping is a detailed visualization of all the steps of the work process and visualization of tasks in a single glance.
- Assign responsibility: The key to timely completion of the activity is to assign it to the responsible person and make them accountable for the task.
- Determine resource and plan budget: Resource planning is a systematic way to get the optimum utilization of time and people. For any implementation, budget planning is critical. The budget is not only the money but also time to complete the task.
- Risk assessment and mitigation strategy: While planning any actions as an outcome of proposed CAPA implementation, the risk with respect to upstream and downstream processes needs to be evaluated. The action taken to eliminate or prevent issues or events should not end up with additional issues or conflict already implemented systems. In case of any potential risk identified, an adequate mitigation strategy should be in place alongside the implementation plan.
- Change management process: Any changes to be made in the system must route through defined Quality Management Tools or Change Management process or Change Control process.
Step 7: Closure and effectiveness review
Closure and effectiveness review is an important step to evaluate actions taken. It’s divided into sub-steps.
- Verification of action completion
- Effectiveness verification of implemented Corrective Action and Preventive Action
Verify and Validate
As per the guidance, – 21 CFR 820.100(a)(4), implemented corrective action and preventive action needs to be verified or validated to ensure that the implemented remediation actions are working as intended and do not have any negative effect on the quality system.
- Verification or validation should be done with documented evidence
- The generated data should be reviewed to ensure the adequacy of the data
- The effectiveness of the implemented corrective action and preventive actions should be reviewed to ensure that a similar quality issue does not exist
To verify the closure of the Corrective Action and Preventive Actions (CAPA) you should ask the following key questions:
- Are all the proposed actions implemented as planned and outlined in the action plan?
- Is the implementation done through a proper change management system and documented?
- Relevant training and communications have been completed?
To validate the effectiveness of the implemented Corrective Action and Preventive Actions (CAPA) you should ask following key questions:
- Is the objective of action proposal is been met?
- Is any change resulted in another adverse event?
- Is sufficient amount of data available to validate the implemented CAPA?
KEY – Verify the changes with evidence and document it
Effectiveness verification is done to ensure
- The root cause of the problem is addressed
- The issue will not reoccur in future
- No adverse effect noticed on implementation of actions
- Adequate controls or detection mechanism is established
References:
- ICH Q9 and Q10
- ISO 9000:2005 (E)
- 21 CFR 820.100
- 21 CFR 211.192, 21 CFR 211.100, 21 CFR 211.22
- EudraLex – Volume 4 Chapter 1
- COMMISSION DIRECTIVE 2003/94/EC
- www.fda.gov
- www.gov.uk
- http://alvamed.com/about-medtech-compliance-company/newsletter- i. articles/2015-fda-form-observations/
- www.educational-business-articles.com/fishbone-diagram/
- Book; SCAMPER: Games for Imagination Development
- www.mindtools.com